In the face of numerous challenges, working smarter rather than harder is how architecture, engineering, and construction (AEC) firms can stay competitive. Automation and customization is one way to achieve this, with customized design and production workflows offering many benefits . Here, we’ll share some real-world examples of design automation and customization. These case studies demonstrate the transformative potential of technologies such as Visual Scripting, Python API, and Bimplus, and their ability to enhance productivity, efficiency, and collaboration in today’s AEC sector.
Faster Project Deliverables
ALLPLAN’s automated reinforcement detailing tools aid designers in creating reinforcement layouts and drawings swiftly, with built-in intelligence to automatically detect and rectify potential errors or clashes. A practical example of this intelligent automation is the process of modeling shear studs.
With ALLPLAN, designers can simply feed values into an interface, prompting the software to automatically arrange the shear studs around a column, and produce a 3D model of the structure. Coupled with ALLPLAN’s intelligent modeling capabilities, designers can rapidly create an intelligent table that synchronizes with the model. This synchronization ensures precise and consistent information across fabrication drawings and invoicing.
The automation of these processes not only simplifies the design procedure but also minimizes the potential for errors. The results are tangible: improved efficiency, enhanced productivity, and reduced risk of delays in manufacturing or during onsite in-situ construction.
© Philipp Hodel, Zug Estates
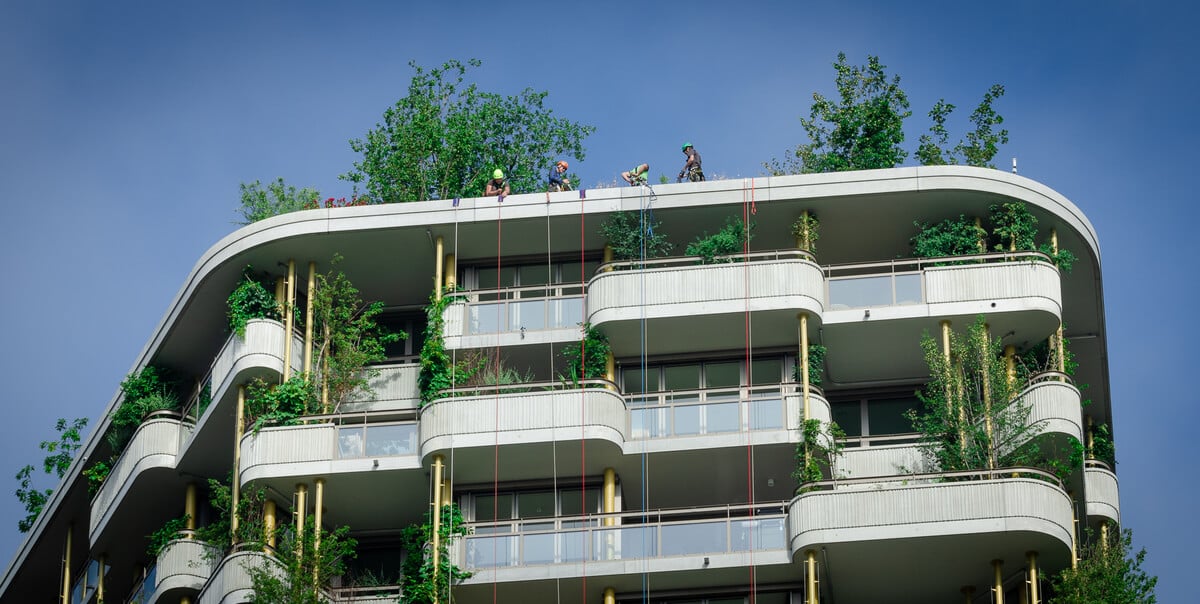
Other applications:
• Parametric modeling of flexible, customizable models, like precast vaults/chambers or staircases
• Adjusting and re-drawing imported plans automatically with Visual Scripting
• Converting objects into intelligent precast elements
• Automating the creation of standardized bridge elements or precast bridge components
• Parametrically creating openings in walls, slabs, or other elements
Automating Repetitive Workflows
Visual Scripting and similar customization tools have been instrumental in minimizing repetitive and often time-intensive tasks. A case in point is the creation of shop drawings, where automation has resulted in significant time efficiencies.
Once the modeling and detailing stages are complete, ALLPLAN simplifies the creation of a comprehensive set of documents. With a single click, ALLPLAN software generates shop drawings for all precast components – including reinforcement, fixtures, and dimensions – using intelligent, custom templates rather than a standard scheme. Designers can effortlessly extract legends and schedules from the model to be directly placed onto the drawings, using either the provided templates or their customized versions. Layouts can be individually created, or multi-page shop drawings can be batch processed with ALLPLAN, ensuring headers and title block information are always current.
ALLPLAN’s unique integration of 2D and 3D technology marks a significant advancement in design efficiency. This technology allows designers to work in a model- and plan-centric manner, where the plan isn’t merely a 2D representation, but a view of the model itself. This synchronicity ensures 100% consistency between the model and plan, offering increased flexibility and customization. Consequently, changes made in the plan automatically update in the model and vice versa, leading to substantial productivity gains for designers, engineers, and manufacturers.
Other applications:
• Automated bills of materials or schedules that update as the model changes
• Efficiently allocating tasks to team members
© ALLPLAN GmbH, Munich; ALLPLAN Bridge already provides integrated parametric modeling, analysis, code-based design, and detailing.
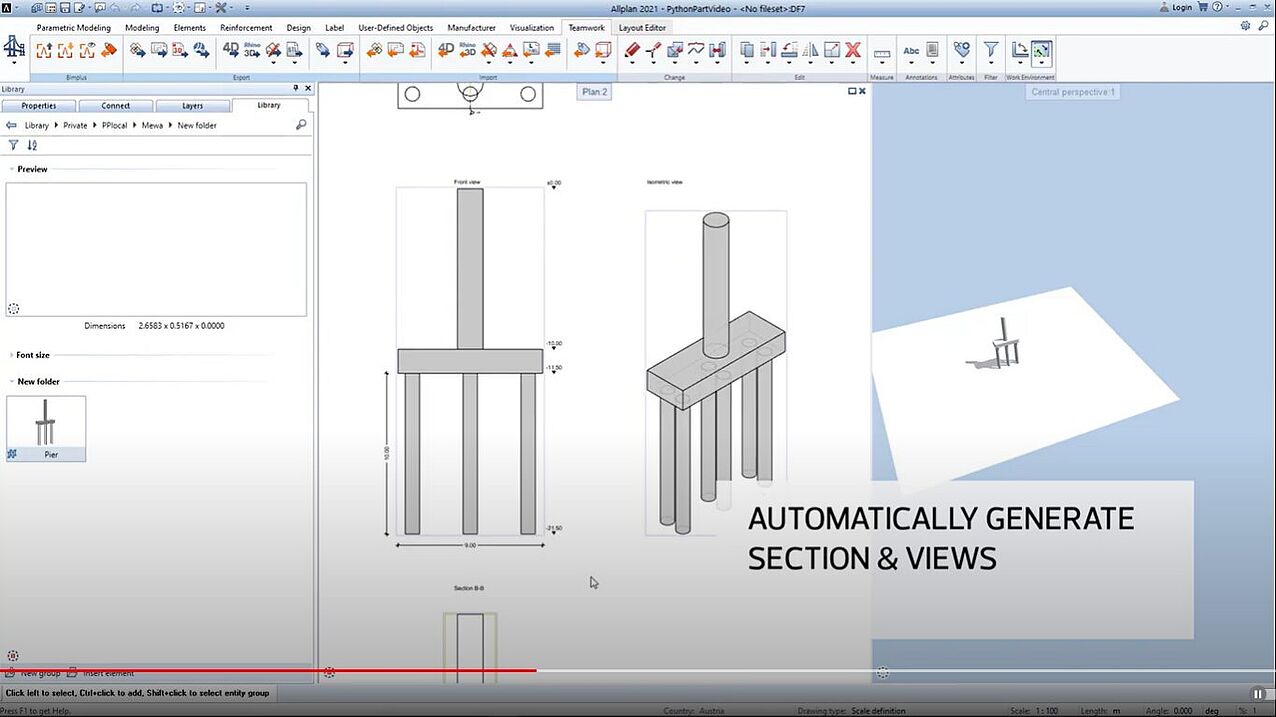
Better Quality Checks and Validation
Customized solutions offer immense utility in validation and checking procedures, such as compliance checks for specifications, quality standards, and safety concerns. ALLPLAN also provides various interfaces that automate this within the precast plant, ensuring consistent supply of quality-assured data.
Take MWS-Connect, for instance. It allows designers to generate reinforcement optimized for production, creating technically correct data for production automatically. With machine options considered within the CAD system, designers work with the correct, pre-set machine parameters. This ensures a smooth, error-free transition from the design phase to production, greatly enhancing the overall project efficiency and quality.
Other applications:
• Automated modeling validation tools that identify and resolve conflicts and errors, or check against specified requirements such as building codes and regulations
• Modifying IFC objects based on pre-defined rules in a .CSV file
© ALLPLAN GmbH, Munich; ALLPLAN automatically generates shop drawings for all precast elements, including reinforcement, fixtures, and dimensions. The software uses intelligent templates rather than a standard scheme.
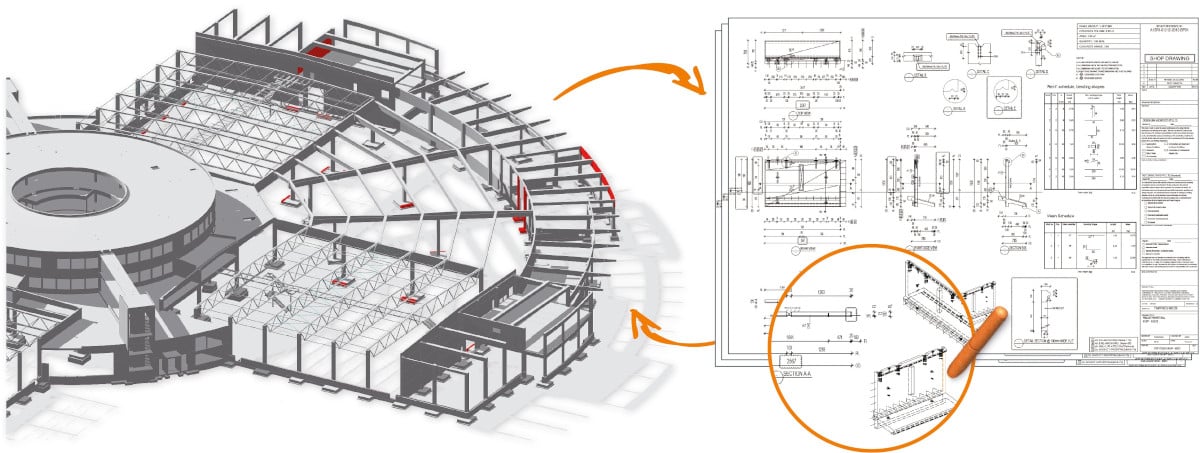
Conclusion
If projects are to be delivered efficiently given the challenges faced by the AEC industry, then automation has a central role to play in achieving this. These examples of reinforcement modeling, automated shop drawings, and quality production data demonstrate how automation not only enhances efficiency and productivity but also significantly reduces error margins. For more inspiration and practical application examples of these tools, download Part 2 of our Design Automation whitepaper: "10 Practical Examples of Automation."