A new tunnel is to be built to relieve the chronically congested Basel city highway. The Basel Rhine Tunnel will provide a link between the Hagnau and Wiese junctions. Scheduled for completion in 2029, the tunnel will include a two-lane tube in each direction at a cost of 2.36 billion Swiss francs. Rapp AG is a member of the Basilea engineering consortium (partners: Gruner AG, movIng AG, Bänziger Partner AG) and is working on a large part of the engineering structures in front of the tunnel portals on behalf of the Federal Roads Office, FEDRO. This 10-year project is incredibly complex, which is why Rapp AG have chosen ALLPLAN Bridge as their 3D bridge modeling tool of choice.
Project Background
The new tunnel runs in two directions. From the direction of France/Germany, the tunnel starts at the Birsfelden junction and ends north of the Badischer Bahnhof station. There, the lanes connect to the existing bridge structures. From the direction of France, the Klybeck exit will be used as a connection for the Rhine tunnel. From Germany, a new exit ramp will be built at the existing border bridge. As well as relieving road congestion and increasing safety, the project will also improve noise protection in the area with sound-absorbing cladding and low-noise pavement.
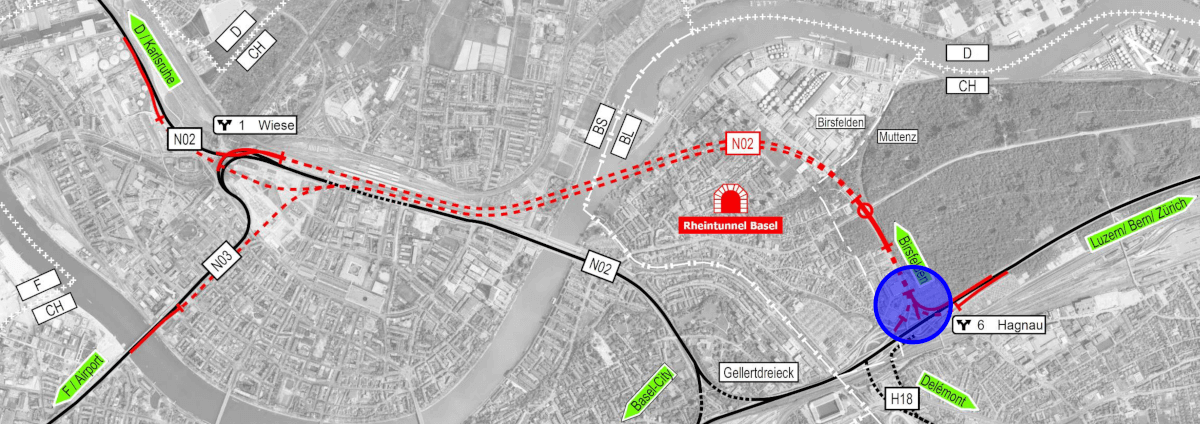
Challenging and Complex
The new artificial structures and the currently existing road alignments lie on top of each other on up to four levels. In addition, the building structure has many complex geometric shapes, which have irregular forms in all directions.
The overpass port railroad is another challenging area. The port railroad is a three-span bridge of around 80 meters in length with a trough cross-section prestressed in the longitudinal direction. In plan view, the structure crosses the new roadway in the direction of the Rhine tunnel in a very circular manner. Adjacent to it are retaining walls with complex geometric shapes. The trough shape of the bridge merges into the retaining wall and its line then runs out in the portal structure of the tunnel.
The overpass is founded on drilled piles, the construction of which is anything but simple. Some of the substructures are being built directly next to an operating rail line within an excavation pit that is around 10 meters deep. In the construction sequence, the new bridge slab will be built next to the operating rail bridge and moved to its final position with a transverse thrust during a four-month closure of rail operations.

3D Modeling Benefits
Given the complicated layout, the 3D model has been of great benefit for identifying spatial collisions for the Rapp AG team. Even at an early stage of the detailed design, there is already a high level of detail in the 3D model. With ALLPLAN Bridge, the complex geometric shapes of the building structure can be processed efficiently within the dynamic design process. In addition, the self-checking, the rapid generation of sections at any desired point and the realistic visualizations also help make the design process much easier.
Parametric design was another important feature of ALLPLAN Bridge that is helping deliver this project efficiently. Thanks to the parametric model, changes are made quickly and efficiently – and there are many changes in projects of this type. A change only has to be made at one point, and subsequently, all elements linked to it are automatically adjusted. Parametric design was also used to easily map the excavations in ALLPLAN Bridge.
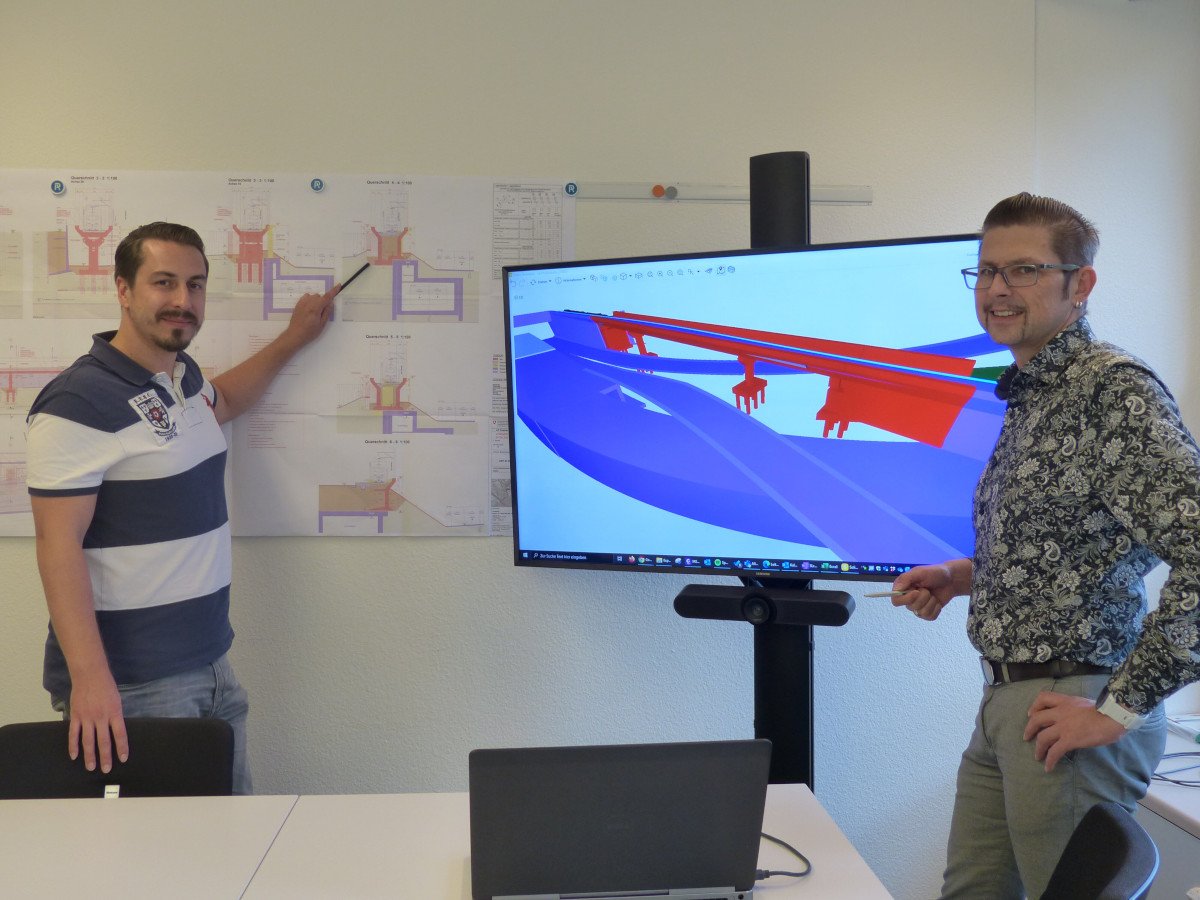
Making the Leap
Rapp AG has been working with ALLPLAN software since 2018. Team leader Larsen Szulerski is more than satisfied with what has been achieved so far: “We have been in an ongoing learning process for the past two years and are happy about any progress. This can be measured not only in terms of improved efficiency, but much more in terms of the new possibilities that ultimately lead to a higher quality of our work. On this path, however, we must have the courage and openness to try out new things. That's the only way we can continue to develop.”