What advantages does prefabrication offer in terms of climate protection?
Little by little, the image of concrete is changing in the context of climate protection. Concrete is no longer merely part of the climate problem, but also an essential part of the solution. Precast concrete elements offer unique opportunities in this context – especially in terms of sustainable production, thermal efficiency, and reusability. We asked Anton Glasmaier, Managing Director of the Association of Austrian Concrete and Precast Plants, for his thoughts on this topical subject. Below, we summarize the most important findings for you in this blog article.
Before we get into the topic of climate protection, it's worth noting that the advantages of precast concrete extend beyond environmental benefits. An essential factor that enhances the effectiveness of precast concrete is the safety it offers to the workforce. The construction industry, known for its high accident rate, has seen improvements thanks to technologies like precast plants. Safeguarded machines take over dangerous, physically demanding, or even unhealthy work steps. So, while the environment significantly benefits from the efficiency and precision of prefabrication, so do the people devoting their time and energy to the development of structures.
With that understanding of how precast concrete enhances safety, let's look at the positive effects of precast concrete in each life cycle, from initial design to the end of its life:
1. Climate protection benefits in the design of the structure
With the help of specialized precast planning tools – like those from ALLPLAN, for example – very detailed planning of the precast elements takes place first. Thanks to numerous automations, this planning is also extremely efficient. ALLPLAN's "design to build" approach means that design feasibility and buildability is considered from the very first moment. Additionally, OPEN BIM reduces data losses and friction between the individual project phases and thus offers the potential to minimize errors and increase efficiency.
Furthermore, thanks to its unique properties, concrete enables better use of space: it is possible to plan and build both in depth and in height, thus reducing the building’s footprint and thus minimizing soil sealing.
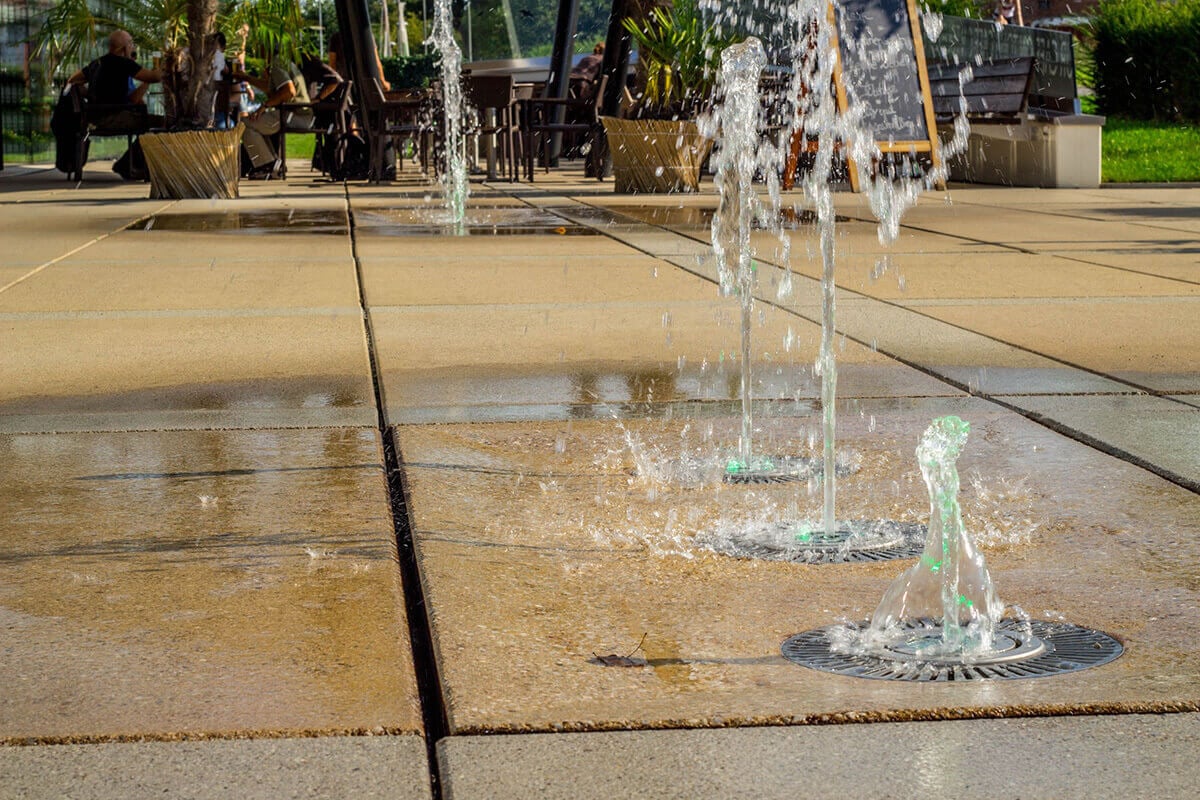
2. Climate protection benefits during production at the plant
The production phase is carried out in a plant in a much more resource-efficient manner than on conventional construction sites. Firstly, there is hardly any waste, since any excess concrete can be reused immediately. Secondly, water can be reused or purified and reintroduced into the groundwater system. In addition, the measuring and distribution of concrete and reinforcement is managed by computer-controlled robots, which is much more precise than manual methods. This precision results in savings in the double-digit percentage range.
Enormous material savings are also possible with hollow-core construction. With hollow-core slabs and walls, around 45% less concrete and 30% less steel is required. Very similar values are possible for precast elements with voids and recesses – everything that is not statically necessary in terms of concrete and steel can thus be saved and brings enormous ecological advantages both in production and transport.
3. Climate protection advantages within the construction processes
After the curing and quality inspection of the precast elements, they are transported to the construction site. Instead of hundreds of trips with concrete mixers over a period of months – as is the case with conventional construction sites – the precast elements can be transported to the construction site within a few days, ready for use, placed in the right position by crane and installed immediately. The noise and dust pollution for the neighborhood and workers is reduced to a minimum. With the help of intelligent software solutions, the prefabricated parts are already produced, loaded, and transported in the correct sequence for installation – which, in turn, reduces journeys to a minimum and speeds up construction processes.
Technologically, there is even some potential here. For example, an intelligent crane could recognize the finished parts with the help of a built-in chip and independently move them to the right position. The advantages are even more time savings and fewer emissions.
Another plus for prefabrication: less waste is produced in the precast plant. A small amount of unavoidable residue, such as plastic packaging from hoses or similar, can be properly and cleanly separated for recycling or disposal.
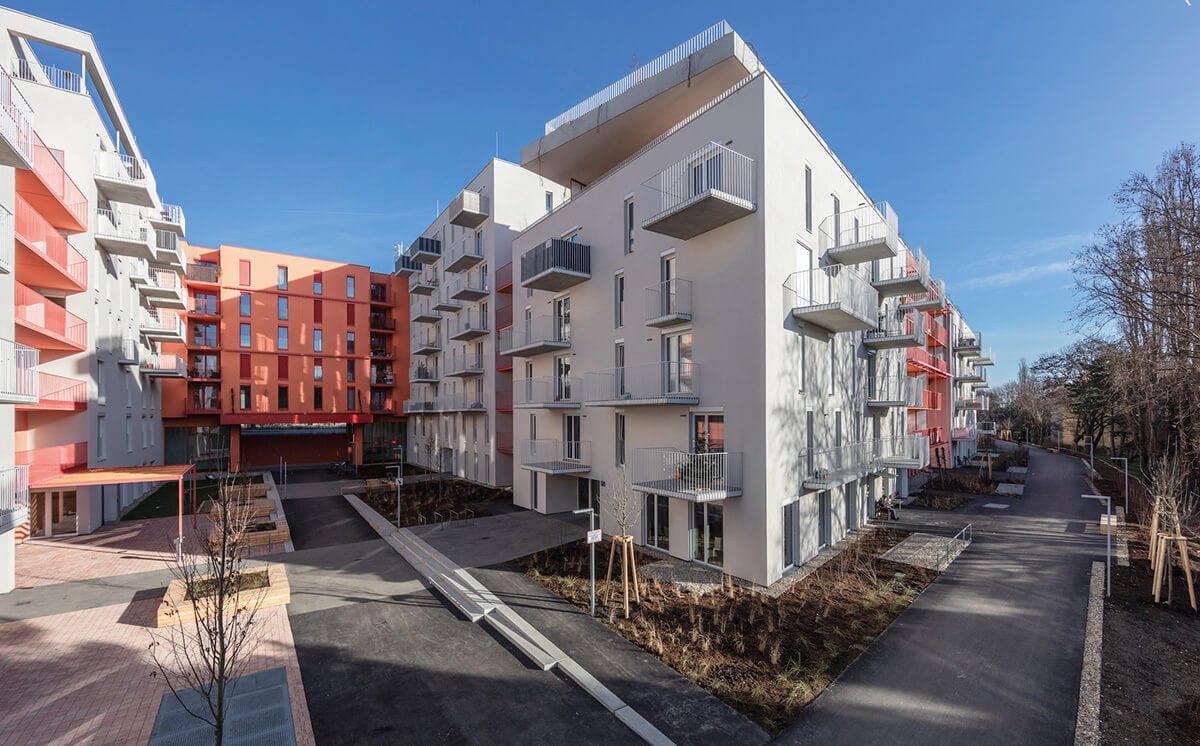
4. Climate protection advantages during operation
Concrete offers enormous thermal advantages and makes it possible to reduce heating and cooling costs – which is one of concrete's greatest strengths in terms of climate protection. "Building component activation" is the keyword here. One example is the Liselotte-Hansen-Schmidt educational campus in the Urban Lakeside Aspern, a school in Vienna with 1,400 students and teachers. Here, more than 50 geothermal probes ensure a pleasant indoor climate. The heat or cold extracted from the ground is conducted through hoses integrated in the precast concrete elements. The precast elements thus store the energy and slowly release it into the rooms. Component activation becomes particularly useful when several buildings interact in terms of energy. The company Hacon is demonstrating this with the "PlusEnergieQuartier21" in Vienna. There, three buildings are combined to form an energy network and the energy is directed to where it is currently needed. One example is the waste heat from the commercial businesses is used to heat water for the neighboring apartments – a win-win situation for all involved.
5. Climate protection benefits during deconstruction or reuse
Prefabrication also offers tremendous benefits in reuse. If one wanted to deconstruct a building after 50 years, it would be technically possible to reuse solid walls, hollow planks, stairs, etc. without further ado. With the help of a digital twin, there would be transparency regarding concrete quality, age, condition, etc. Built-in chips, such as those already used in tunnels today, can sound an alarm when loads are above a certain level. Companies looking to buy or sell components come together via exchange markets, as is already practiced for windows or door leaves. The legal framework for this area has not yet been fully clarified – which an important issue, since the reuse of complete, finished elements is much more resource-efficient than recycling. Speaking of recycling: concrete is 100% recycled in Austria – granulated as admixture for new concrete projects or as fill material for paths and roads.
All in all, concrete, especially in precast construction, offers numerous ecological advantages. However, it should not be forgotten that the cement required for concrete production has a very unfavorable CO2 balance. Here, researchers are working flat out to reduce the need for cement and find more environmentally friendly substitutes or additives.
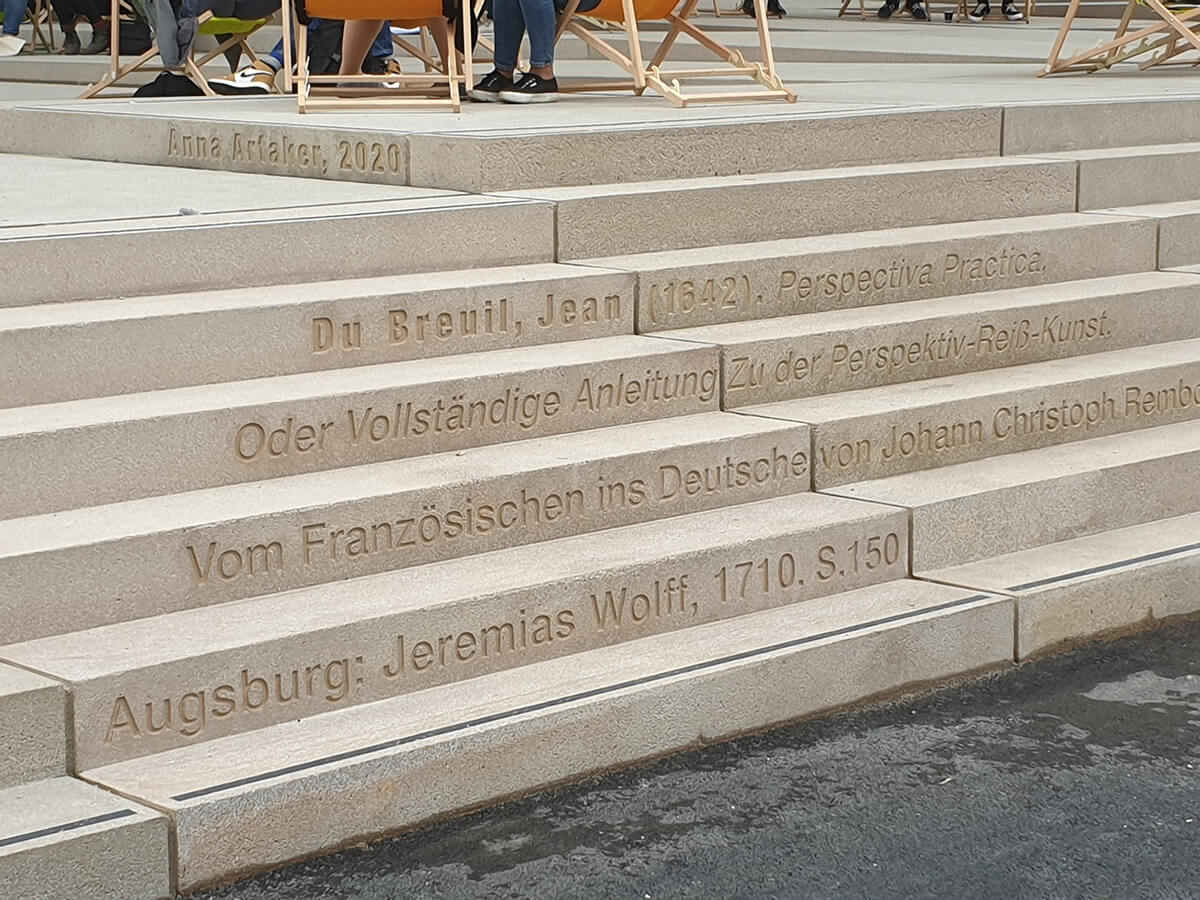
So, will precast concrete be the ultimate solution to our climate problems? Concrete alone will not be the solution, nor will any other material on its own. Climate protection can only work in tandem. The future will be hybrid. Each building material, whether wood, concrete, brick or glass, has particular strengths and should be used in such a way that optimizes and showcases their individual advantages to their fullest potential. A good example of the sensible dovetailing of the advantages of concrete and wood are composite ceilings – here and in many other areas, experts expect further product innovations and increasing use in the coming years.
What is the future of precast construction? The growth figures clearly indicate that the development of precast concrete construction will be positive, innovations will further improve the climate balance, and, in combination with intelligent spatial planning, concrete can help to reduce soil sealing due to its inherent ability to facilitate vertical construction. Its thermal properties, i.e. the slow absorption and release of heat or cold, enable the sensible use of surplus eco-electricity. For example, excess electricity produced during particularly sunny and windy periods can be used to efficiently and sustainably air-condition buildings via building component activation, using hoses integrated into concrete components.
At ALLPLAN, we are excited to be part of the precast market – one of the most innovative and fastest growing segments of the construction industry. Our software solutions provide workflows specifically for the needs of the precast industry, helping to make design more convenient, faster, and error-free.
We would also like to thank Mr. Glasmaier for his insights and ideas around this interesting topic.