Celebrating Structural Ingenuity: Highlights from the SDS2 2024 Solid Steel Awards
High-rise buildings have become iconic symbols of modern urban landscapes, representing both architectural ingenuity and the relentless push towards vertical expansion in densely populated cities. However, the construction of these towering structures comes with numerous challenges that require innovative solutions and meticulous planning.
At the recent ALLPLAN - Build the Future Summit, industry experts gathered to discuss these very challenges. Among the many standout presentations was one by Tony Poulin, Draft Service Manager at Canam Buildings. With over 30 years of experience and a leadership role in managing a global team of over 400 draftsmen, Tony shared his invaluable insights into the complexities of some of Canam’s recent high-rise construction projects.
The Challenges of High-rise Buildings
Tony Poulin’s presentation highlighted three notable high-rise construction projects that exemplify both the challenges and the innovative solutions employed by Canam Buildings. These projects include the Deloitte Summit Tower in Vancouver, 141 Bay Street (CIBC Square Two) in Toronto, and a significant high-rise in Portland, Maine. Each of these projects presented unique obstacles that required meticulous planning, advanced technology, and collaborative efforts to overcome.
Deloitte Summit Tower, Vancouver
The Deloitte Summit Tower in Vancouver is a striking example of modern architecture, featuring a unique design composed of several cubes oriented in different directions. This 24-story building used 5,680 imperial tons of steel, predominantly detailed by Canam’s office in Manila, with additional support from their Quebec City team. The project faced significant challenges due to its complex geometry, which required intricate truss detailing and the precise coordination of six mega columns. These columns, the heaviest W360 shapes available in Canada, were critical for supporting the structure alongside a stabilizing concrete core.
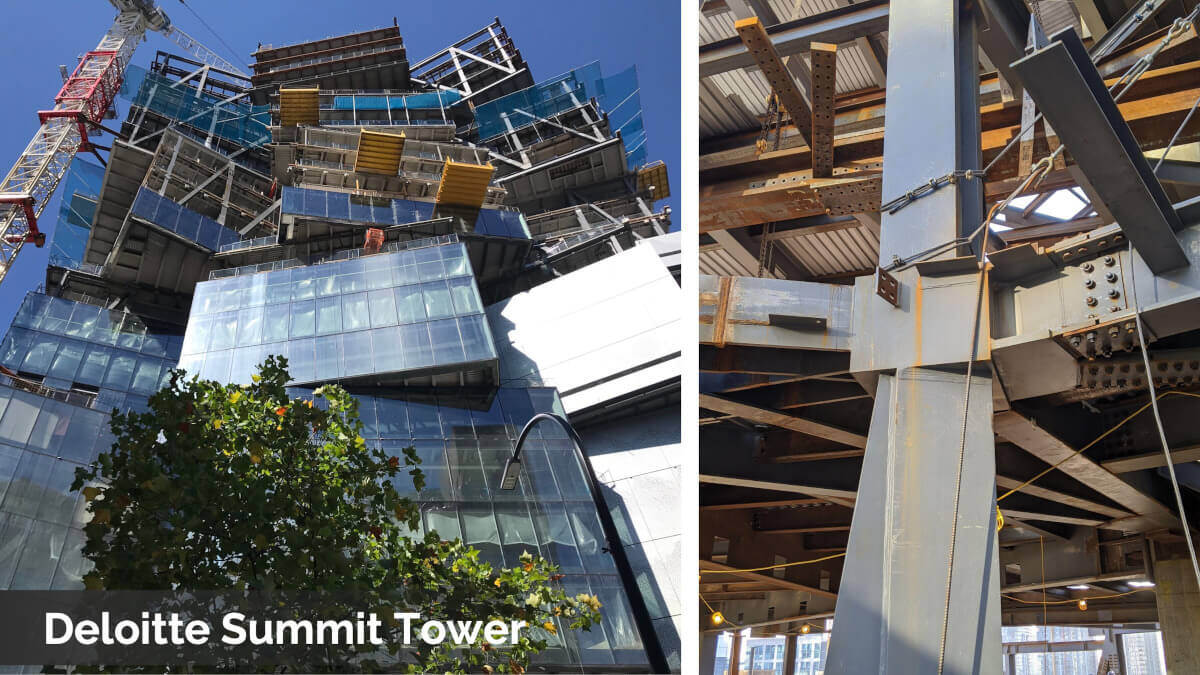
One of the most daunting aspects of the project was the detailing of the four-level trusses, which needed to account for significant camber. The trusses were modeled flat in SDS2 software, with construction lines used to detail the diagonals correctly, ensuring they fit perfectly once the dead loads were applied. Temporary hydraulic jacks were employed to support the cubes during construction, progressively removed as the erection proceeded. The meticulous planning and innovative problem-solving ensured the successful completion of this architecturally ambitious project.
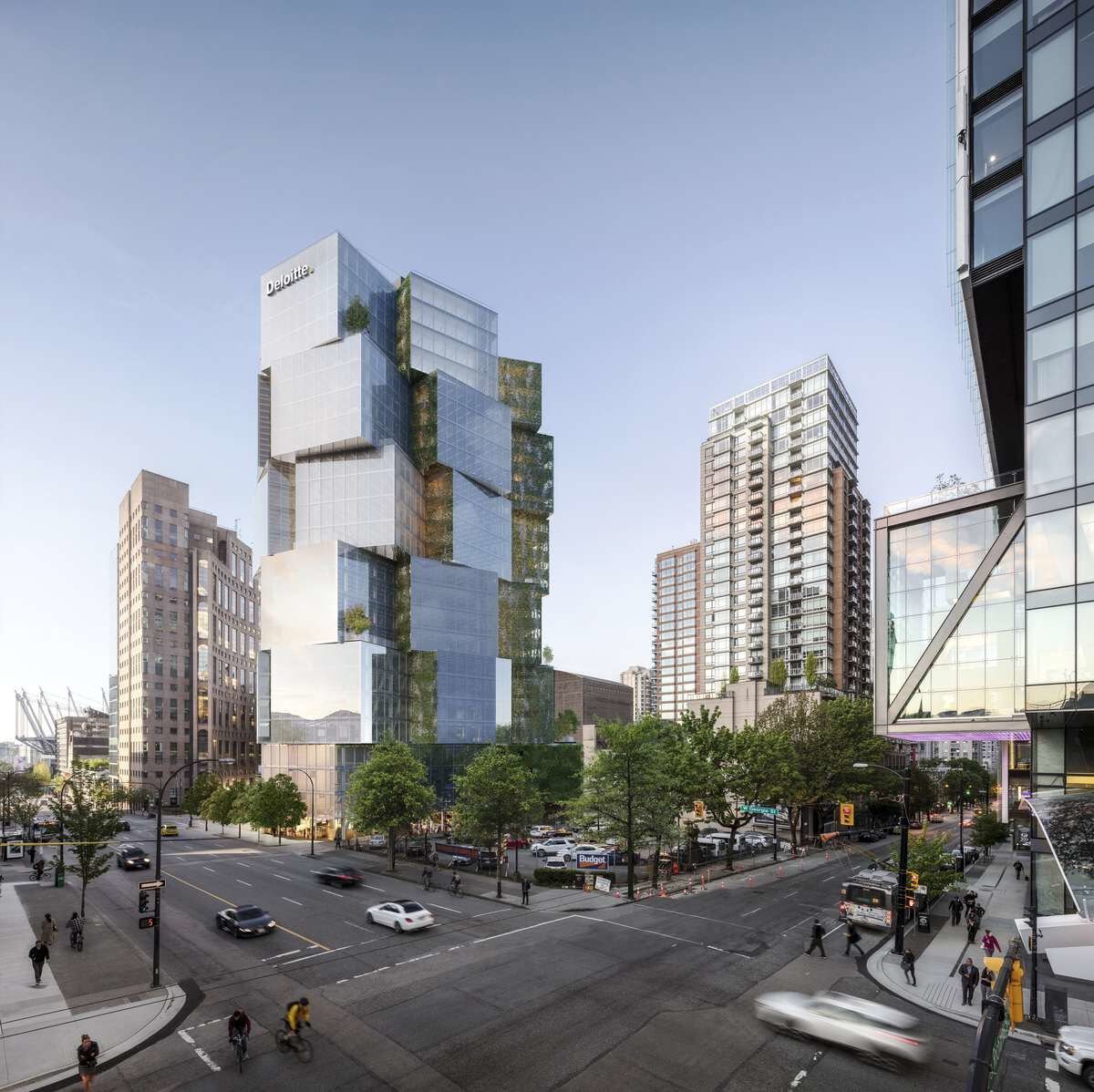
141 Bay Street (CIBC Square Two), Toronto
The 141 Bay Street project, also known as CIBC Square Two, is a 56-story high-rise located in the heart of downtown Toronto. The primary challenge for this project was its construction above active train tracks, necessitating a design with skewed lower columns to provide a smaller base while expanding the building’s footprint above the tracks. The logistical challenges of maintaining train operations while erecting the lower floors required construction to be limited to a narrow window between 1am and 4am.
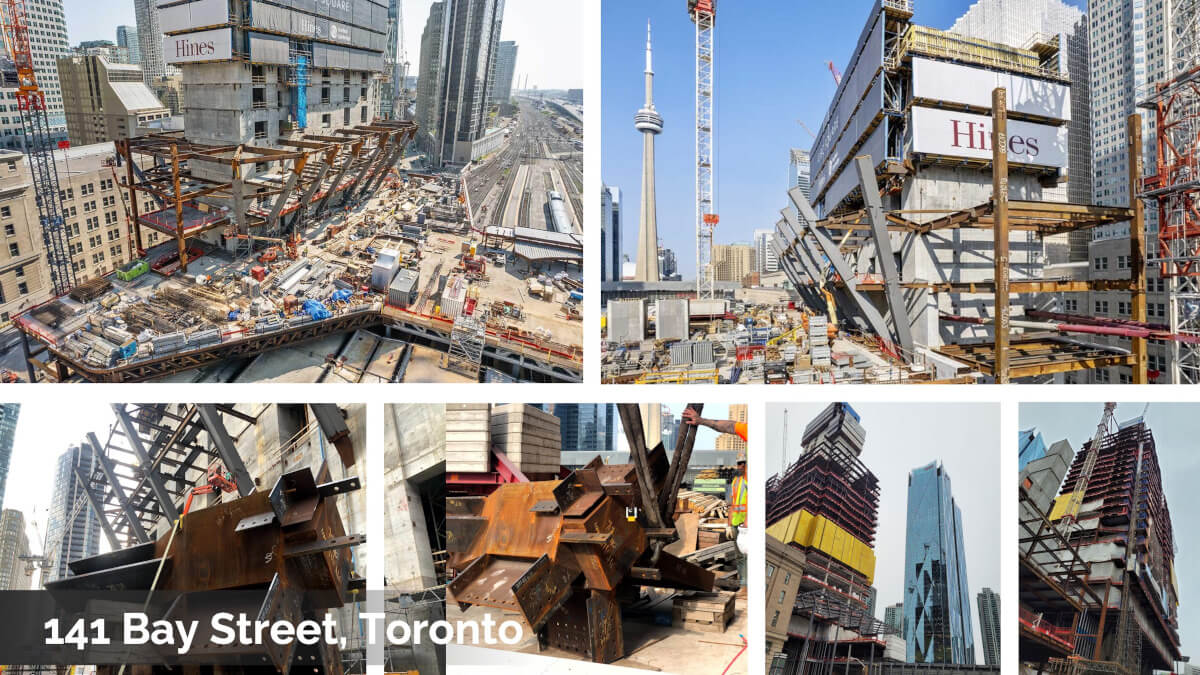
To overcome these obstacles, Canam used a daily model transfer from one server in Manila to another in Québec City, as virtual desktop infrastructure (VDI) was not yet implemented in their Manila office at the start of the project. This approach allowed for seamless coordination and the massive model was efficiently managed by splitting it into four parts. The upper floors, after the fourth level, were constructed during the day as they provided shielding for the train tracks below. This project’s successful delivery highlights the importance of strategic planning and advanced technology in high-rise construction.
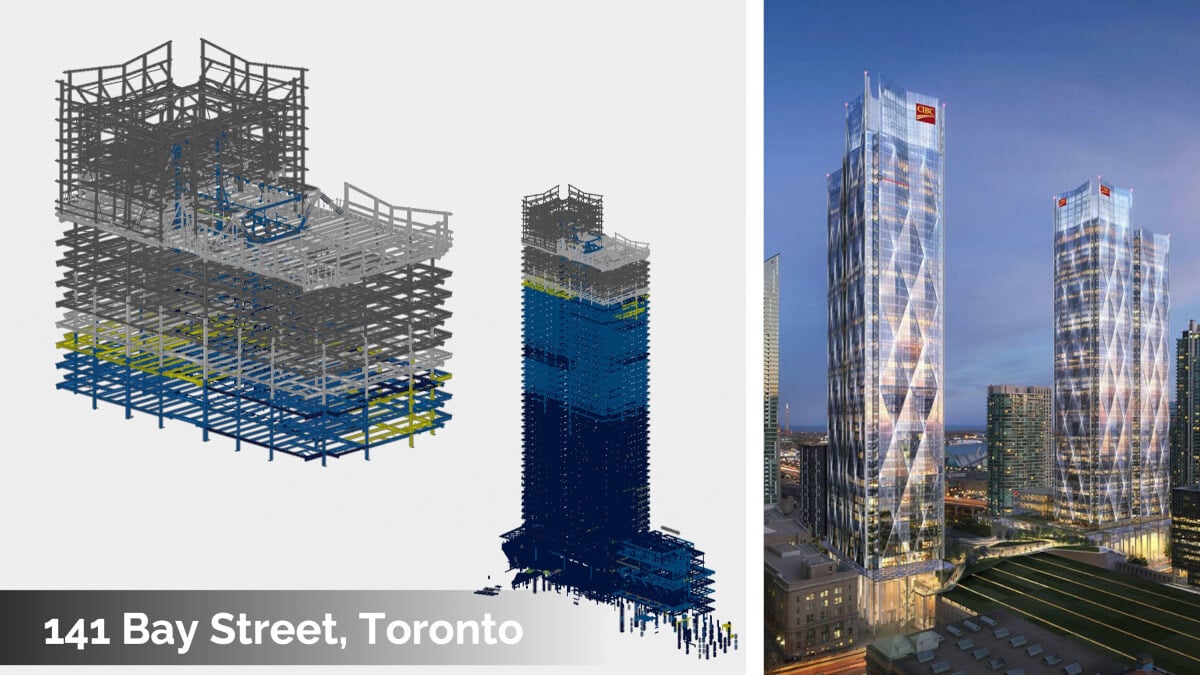
High-rise Building in Portland, Maine
In Portland, Maine, Canam tackled the construction of the tallest building in the state, an 18-story high-rise. This project presented unique challenges due to the absence of a concrete core, necessitating the use of massive steel shapes to form the core. The varying column sizes, from W14 x 665 (pounds per foot) to lighter W10s and W12s, introduced complexities related to steel shortening. The heavier columns could not be shortened as much as the lighter ones, creating potential issues in alignment.
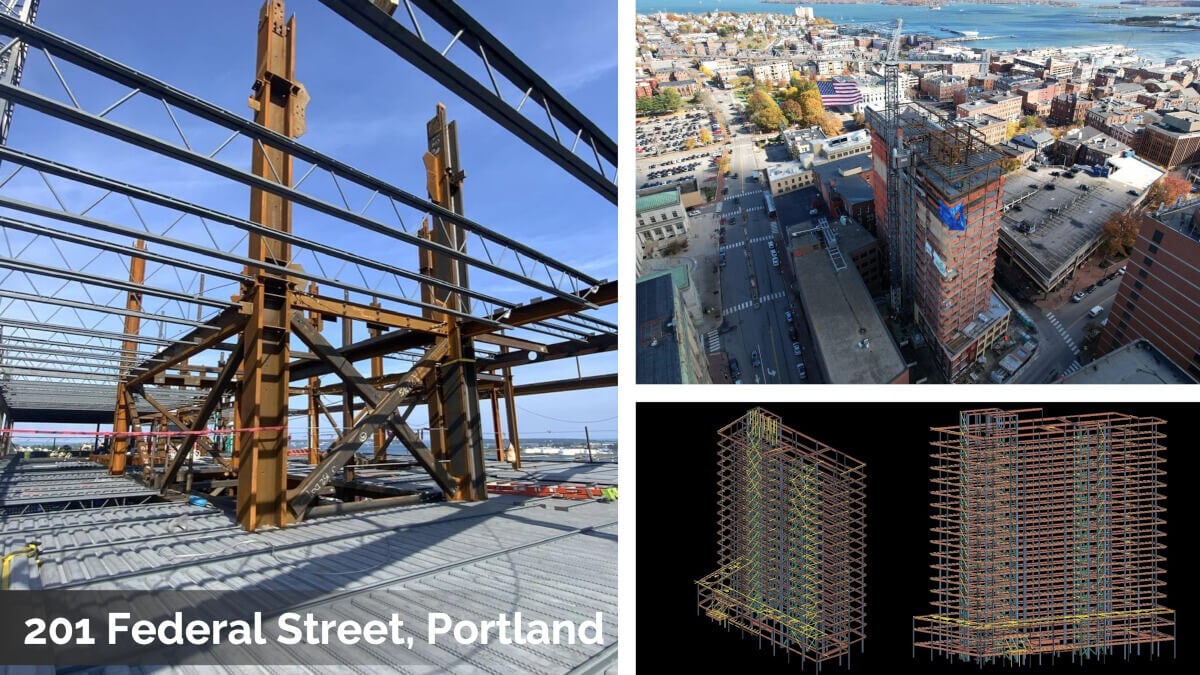
Canam addressed this by graphically modifying the columns in the 3D SDS2 model after the initial detailing process. This approach ensured that the data remained intact for automated equipment and robots while accommodating the differences in shortening. By leveraging advanced 3D modeling techniques and innovative problem-solving strategies, Canam successfully managed the challenges of this high-rise project, ensuring structural integrity and precision.

Building the Future: Lessons in Innovation and Collaboration
These high-rise construction projects undertaken by Canam Buildings showcase the innovative spirit and collaborative efforts necessary to overcome the formidable challenges of modern architecture. From the intricate geometry of the Deloitte Summit Tower in Vancouver to the logistical complexities of 141 Bay Street in Toronto, and the structural innovations in Portland, Maine, Canam has demonstrated an unwavering commitment to excellence.
Through advanced technological solutions like SDS2 modeling and virtual desktop infrastructure, Canam ensures precise detailing and real-time collaboration across global teams. Innovative techniques and adaptive strategies have enabled them to tackle unique construction challenges, from managing steel shortening to coordinating construction around active train tracks.
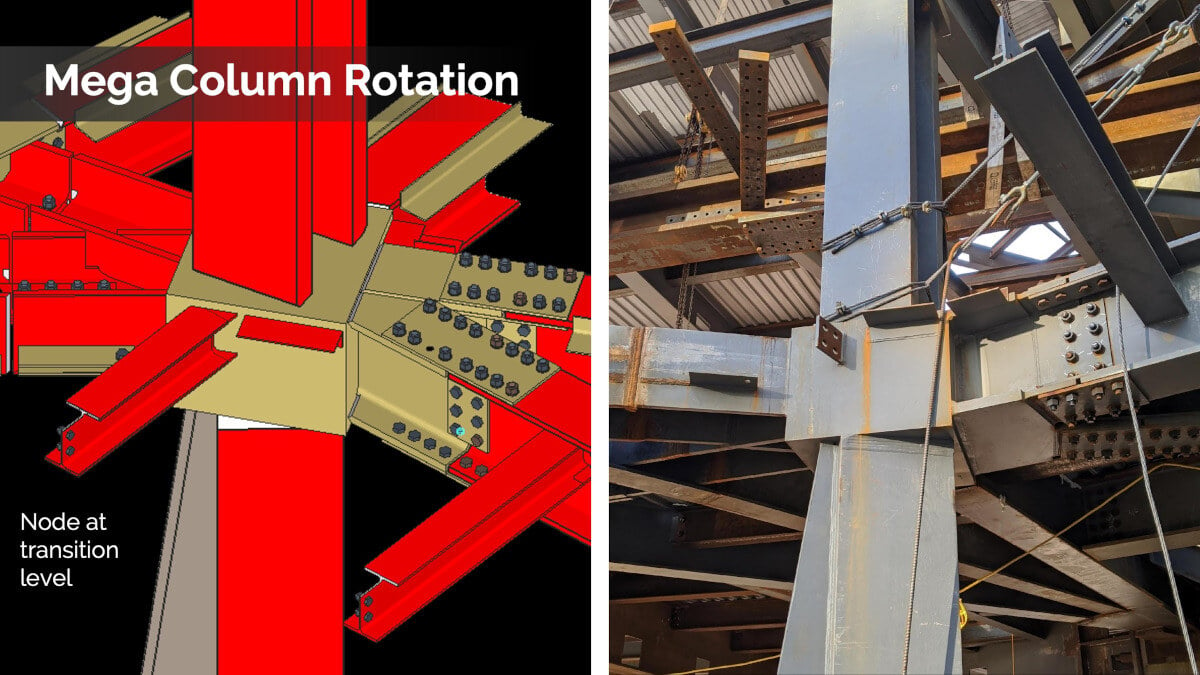
The success of these projects underscores the importance of teamwork, continuous improvement, and a forward-thinking approach in the construction industry. As urban landscapes continue to evolve, the lessons learned from these high-rise projects will guide future endeavors, setting the stage for even more ambitious and groundbreaking structures.
About Canam Buildings
Founded in 1961, Canam Buildings has grown into one of North America’s largest structural steel and steel joist fabricators, handling around 8,000 projects annually across Canada and the United States. With a production capacity of 380,000 tons per year, Canam’s main plant in Saint-Gédéon, Quebec, spans 700,000 square feet and includes 14 specialized shops. Their product range includes prefabricated load-bearing walls and various steel construction products, supported by an efficient fleet of delivery trucks and trailers.
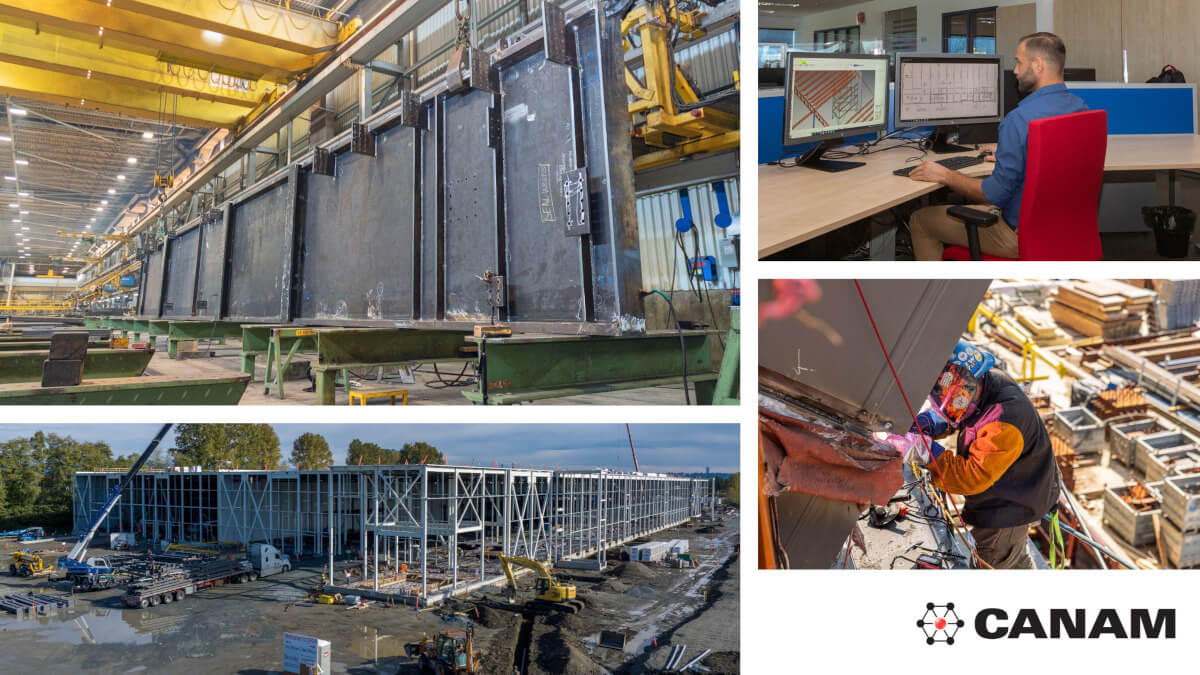
Canam’s global footprint extends to three international offices in Kolkata, India; Manila, Philippines; and Brașov, Romania. The Brașov office, which recently celebrated its 25th anniversary, plays a crucial role in their operations with 435 employees. Canam’s innovative projects span from small buildings to large sports stadiums and significant infrastructure projects, such as the new bridge between Windsor, Ontario, and Detroit, Michigan.