According to UN estimates, 70% of the world's population will be living in cities by 2030. Could industrialized construction and mobile prefab factories be one of the ways to solve the global housing issue?
Today, more than half of the world's population already lives in urban areas. The UN predicts that by 2030, more than 5 billion people will live in cities. While this rapid urbanization enables economic growth on the one hand, it also brings with it numerous problems: the emergence of slums, a lack of sufficient waste disposal facilities, inadequate public transportation, increased air pollution, and unplanned urban sprawl, to name just a few examples.
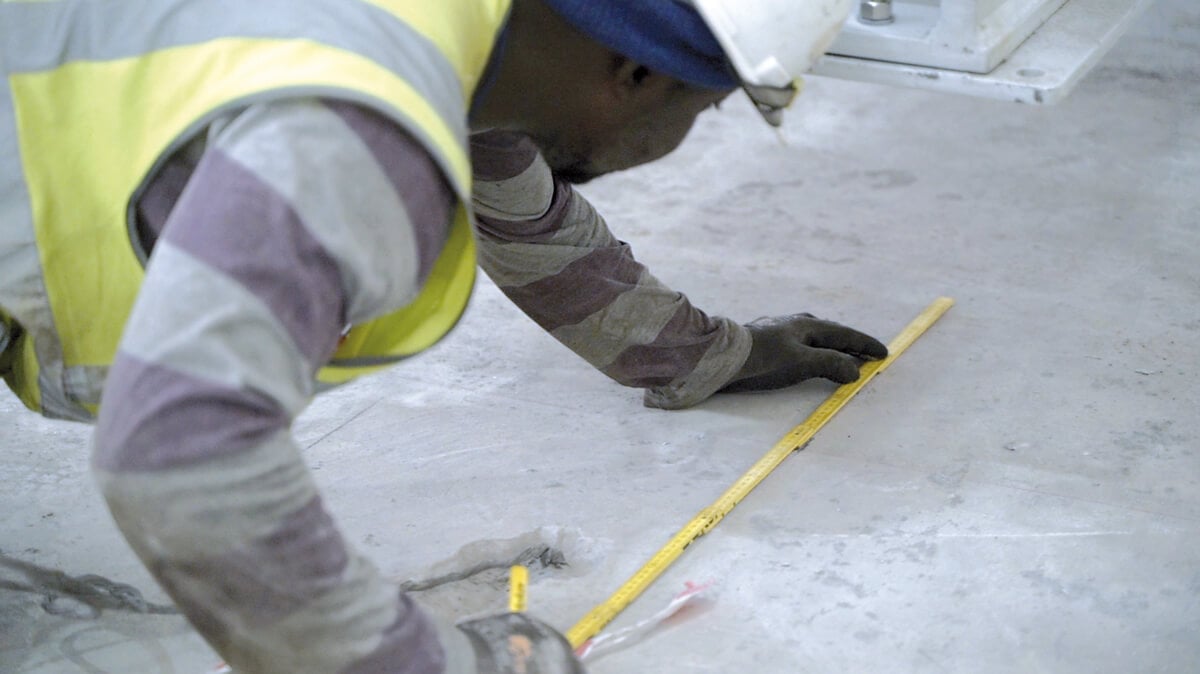
Social housing for the countries of the South
With the 2030 Agenda, the UN has set 17 Sustainable Development Goals (SDGs) to promote peace and prosperity worldwide while protecting our planet. Number 11 is dedicated to cities and human settlements and aims to provide safe, sustainable, and high-quality housing.1
To meet this growing demand for affordable housing in cities, governments in Asia and Africa are increasingly discovering the benefits of industrialized construction. In prefabrication, the production of walls, ceilings, and structural precast parts in precast factories enables time and cost savings. The high-quality parts are then transported to the construction site and erected. However, many countries lack the necessary factories, infrastructure, and technical know-how.
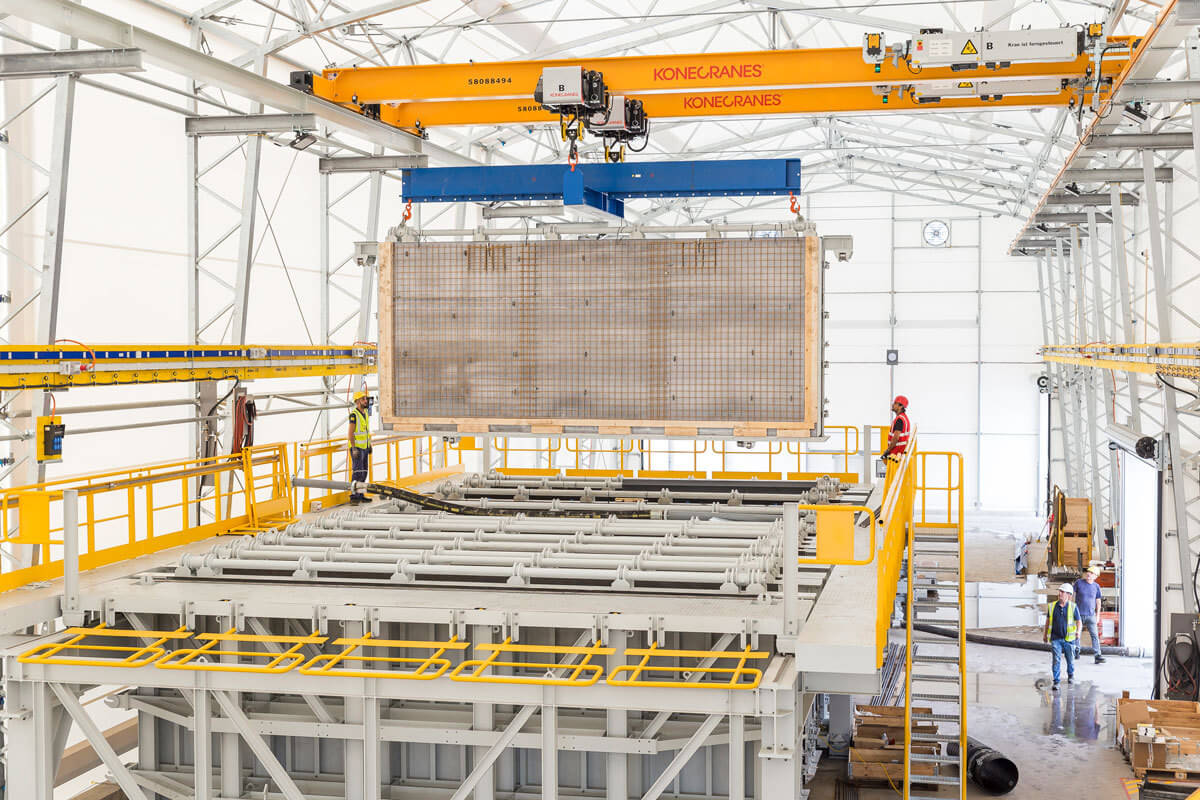
Efficient construction with the mobile precast factory
NEULANDT GmbH, part of the Umdasch Group Ventures, develops innovative solutions for precisely these global challenges in the construction industry. One example is the NEULANDT 3P (Portable Precast Plant), a mobile precast factory that can be used to produce precast concrete elements at any location. The factory fits into 40 shipping containers and is ready for use within four to six weeks. The hall is 70m long and 15m wide and has two integrated cranes with a capacity of 12.5t each.
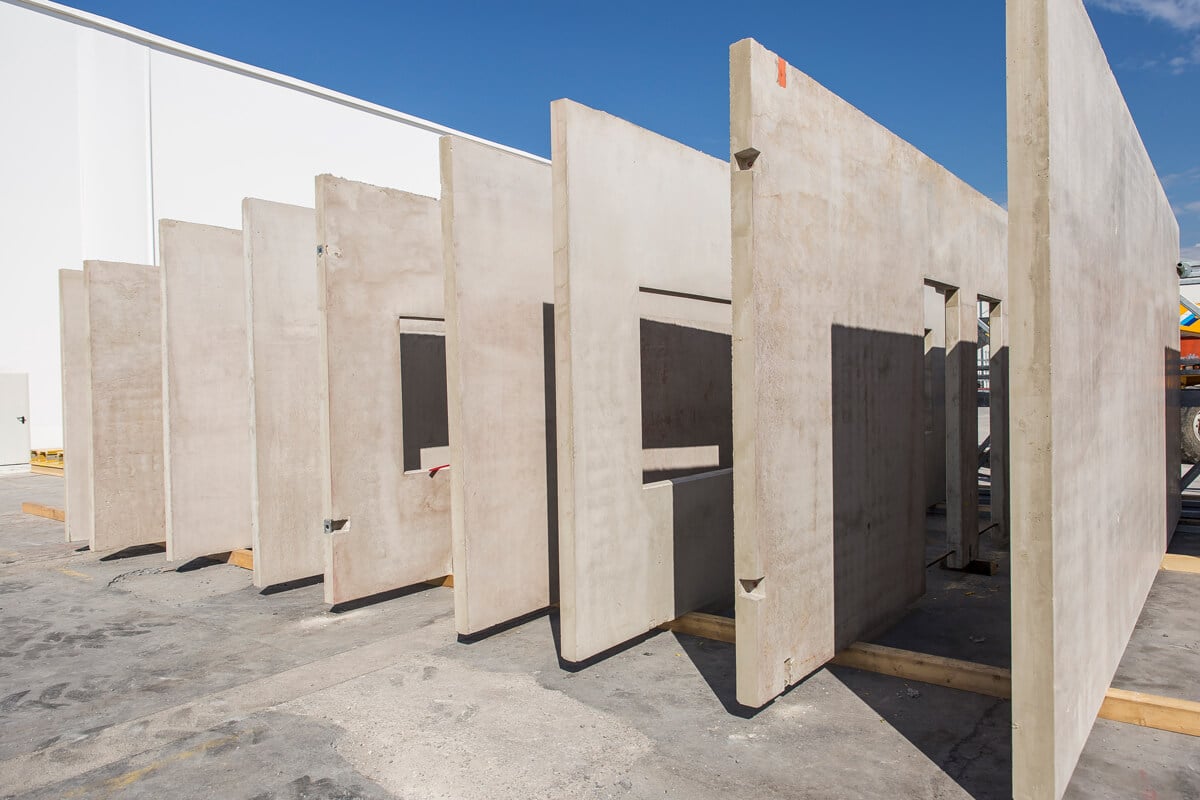
First mobile precast plant successfully assembled
The first mobile N3P production line was successfully set up in Abidjan (West Africa) and will soon be put into operation. In the following months, it will be able to produce up to 1000m2 of precast walls per day.
The efficient butterfly formwork is used in the production itself. This space-saving formwork method uses folded steel formwork structures, which means that the elements are smooth on both sides and require no finishing. Butterfly technology also offers the advantage of faster and more ergonomic formwork operations. After filling with concrete, the initial curing takes place in the battery mold and after a drying period of about 14 days, the precast elements are ready for assembly.
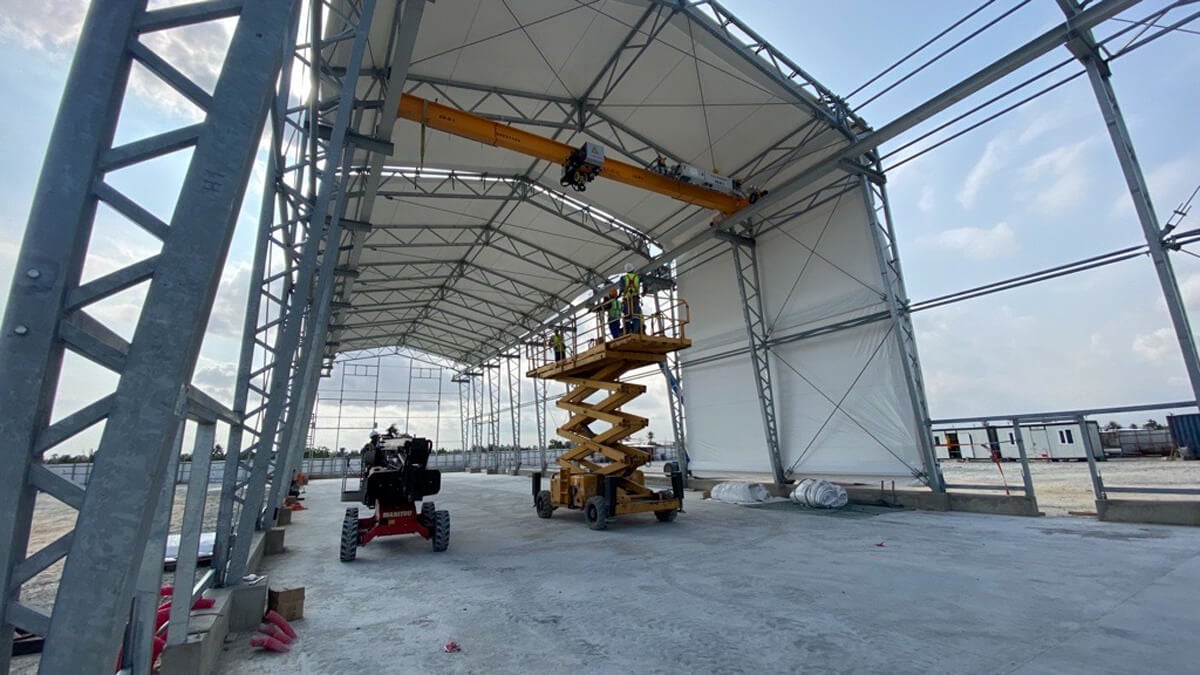
Local production creates local value
The factory produces prefabricated parts with any dimensions between 3.00m x 7.03m and a thickness between 8 and 20 cm. Thanks to its high productivity, the plant is expected to produce up to 300,000 square meters of high-quality prefabricated elements per year, equivalent to more than 1,500 family housing units (based on 65 square meters of living space). These prefabricated units can also be used to construct multi-story buildings. In addition to the focus on social housing, other types of buildings such as schools, hospitals, industrial buildings, or noise barriers are also possible.
Another important aspect is that the added value stays in the region. For this reason, construction companies source raw materials from the region and rely on local labor and subcontractors such as electricians and plumbers. Short transportation routes and optimized logistics processes in turn save time and money and minimize the carbon footprint.
The CAD design of the precast elements is also carried out by regional design offices. The machines in the NEULANDT 3P mobile precast factory are compatible with the most common precast design and detailing solutions, such as ALLPLAN Precast.
Mobile precast factories could be used to build social housing on a large scale at low cost. In this way, industrialized construction could contribute to achieving the goals of Agenda 2030, improving the living conditions of the local population, creating local jobs, and providing sustainable economic activities in the region.