What’s the secret behind STÄBLEINARCHITEKTEN’s successful building projects? As it turns out, it’s their innovative approach to technology. Renowned for their unwavering commitment to innovation and sustainable design, this German architecture firm has consistently pushed the boundaries of what’s possible in the built environment. A key factor behind their success lies in their pioneering role in digitalization, particularly in the realm of Building Information Modeling (BIM) and 3D scanning technologies. By seamlessly integrating these cutting-edge tools into their workflow, STÄBLEINARCHITEKTEN has unlocked a new level of precision and efficiency in their projects – and closed the seemingly inevitable as-built gap between design and construction.
The challenges of refurbishment projects
Refurbishment projects present a unique set of challenges compared to new construction. STÄBLEINARCHITEKTEN, in their diverse portfolio of projects, encountered several recurring obstacles. A primary issue was the lack of accurate as-built data, making it difficult to create precise plans and designs. This was particularly evident in projects like the refurbishment of a pharmaceutical production facility, where complex technical installations and ongoing operations added layers of complexity.
In the case of a multi-story residential property refurbishment, the challenge lay in efficiently surveying the existing building without disrupting residents or resorting to costly scaffolding. Similarly, the conversion of a historic churn barn presented the need to meticulously document and preserve the building’s heritage while modernizing its functionality. Each project, with its unique constraints, highlighted the critical need for accurate and efficient data collection and planning in refurbishment endeavors.
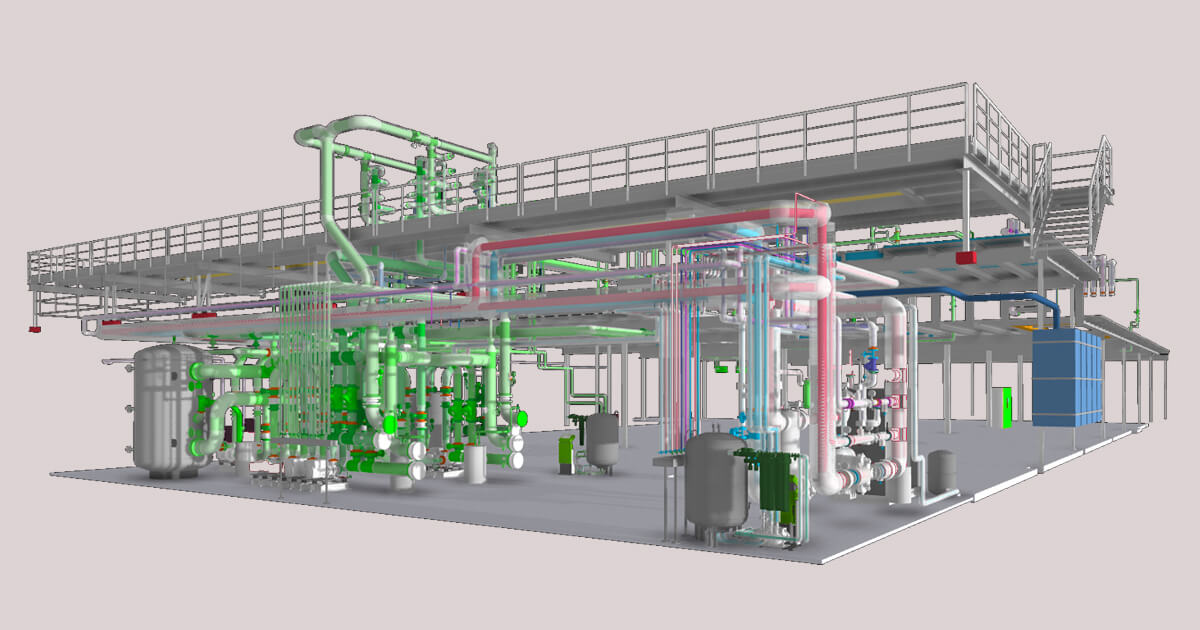
Embracing digital planning
STÄBLEINARCHITEKTEN has long been a supporter of Building Information Modeling (BIM) in their design and planning processes. At the heart of their BIM workflow is ALLPLAN’s powerful architectural design software. ALLPLAN empowers the firm to create comprehensive and accurate 3D models of their projects, facilitating better visualization and coordination among project stakeholders. From conceptualization to construction documentation, ALLPLAN ensures a seamless flow of information and a higher degree of accuracy throughout the project lifecycle.
However, there was still a need to ensure accurate as-built information was recorded during construction, particularly on refurbishment projects. Recognizing the limitations of traditional measurement methods, STÄBLEINARCHITEKTEN turned to Imerso’s 3D scanning technology. By incorporating the Leica BLK360 laser scanner and Imerso app into their workflow, the firm could rapidly capture millions of precise measurements, generating detailed point clouds that offered a comprehensive digital representation of the existing building conditions. This wealth of accurate as-built data allows for better-informed decision-making during the design phase, minimizing the risk of errors and costly rework later in the project.
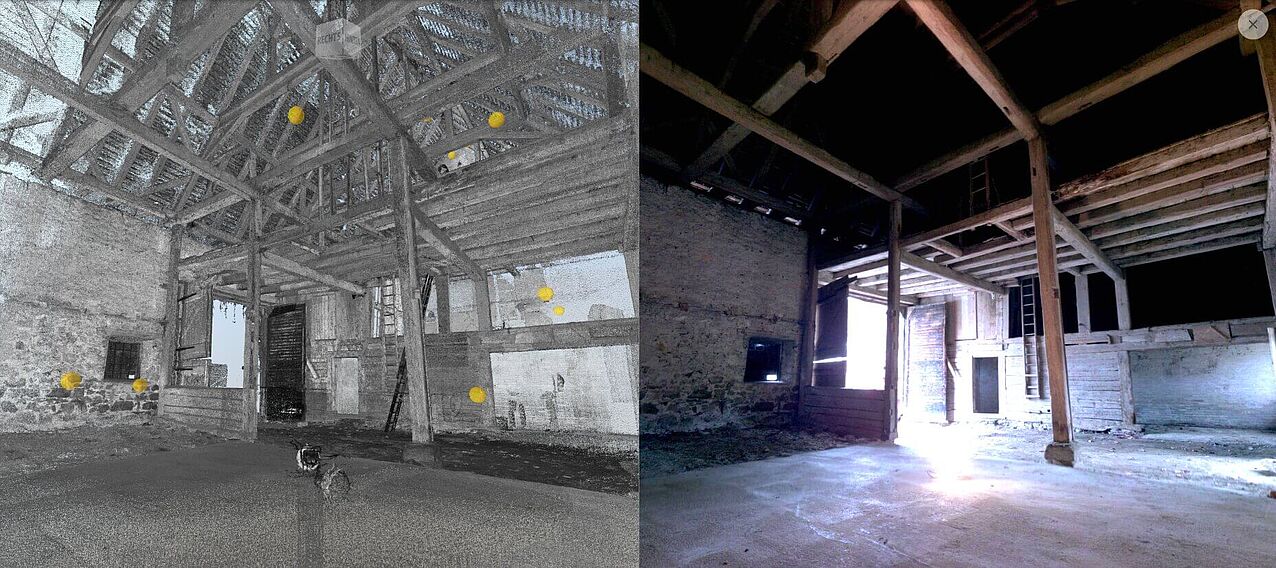
Combining forces for optimal results
Yet the true power of STÄBLEINARCHITEKTEN’s digital workflow lies in the seamless integration of ALLPLAN and Imerso. By leveraging the Industry Foundation Classes (IFC) file format, the firm can easily transfer data between the two platforms. This bidirectional exchange allows the precise as-built measurements captured by Imerso to be directly incorporated into ALLPLAN’s planning models. Additionally, the use of BIM Collaboration Format (BCF) files via BIMPLUS streamlines communication and issue resolution between project teams, ensuring everyone is working with the most up-to-date information.
BIMPLUS is at the heart of digital project data management. Stakeholders form collaborative teams and have access to the latest plans and models, whether they are in the office or in the field. BIMPLUS offers even more functionality to prevent errors. The integrated Solibri plug-in automatically detects design errors in BIM models. The QTO allows material orders, such as concrete deliveries, to be double-checked on site. Professional issue management provides security and transparency so that no task is lost, no design errors and construction defects remain unprocessed, and cost risks due to errors are minimized. The 2D overlay functionality in BIMPLUS visualizes 2D layouts within the 3D model, making it easy to keep layouts and models consistent. This integration of cutting-edge technologies not only increases the accuracy of the design and planning phase, but also promotes a more collaborative and efficient project environment.
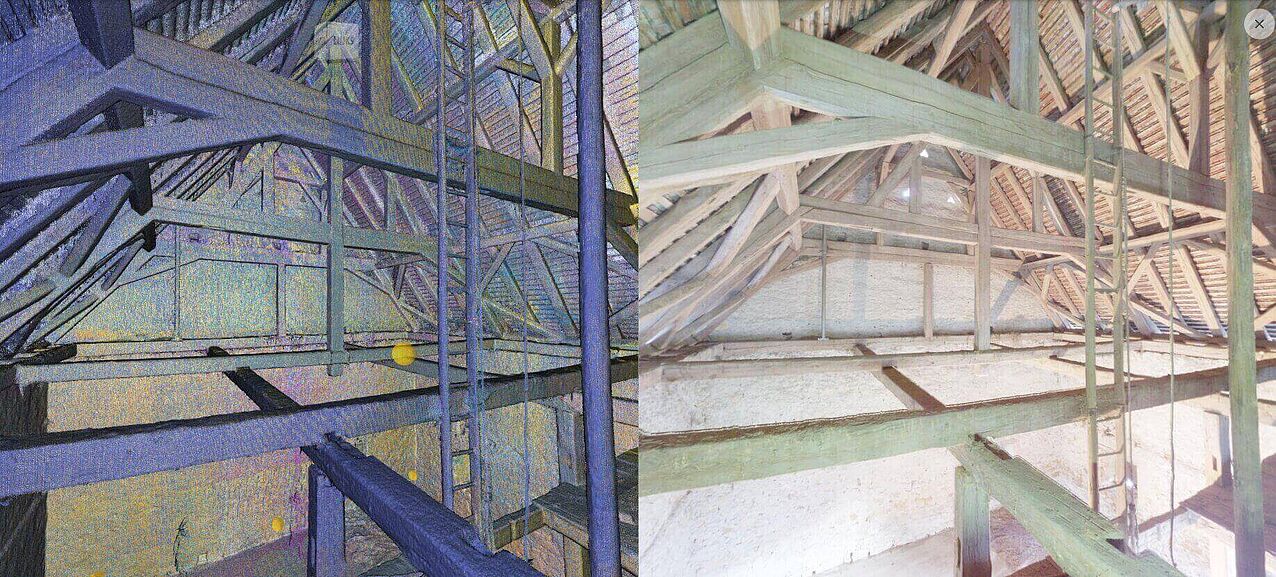
Real-world benefits
The integration of ALLPLAN and Imerso has yielded tangible benefits for STÄBLEINARCHITEKTEN. The firm has reported optimized design choices, more efficient construction processes, and a significant reduction in the risk of costly errors. Ulla Stäblein shared that the mixed reality view in Imerso allows for detailed navigation of the as-built status alongside BIM models, fostering better communication and understanding among project stakeholders. “This streamlined communication has led to fewer site inspections and more comprehensive checks, such as surface and inclination analyses, within the digital twin”, says Ulla Stäblein.
Erhard Stäblein emphasizes the value of digital collision checks, which have virtually eliminated the unpleasant surprises that often arise during construction. “By identifying and resolving clashes in the digital realm, we have achieved smoother construction processes and avoided costly delays. The ability to detect and communicate contextual information directly within the digital twin has also made problem-solving more efficient, while simultaneously capturing accurate documentation of the entire construction progress”, adds Erhard Stäblein.
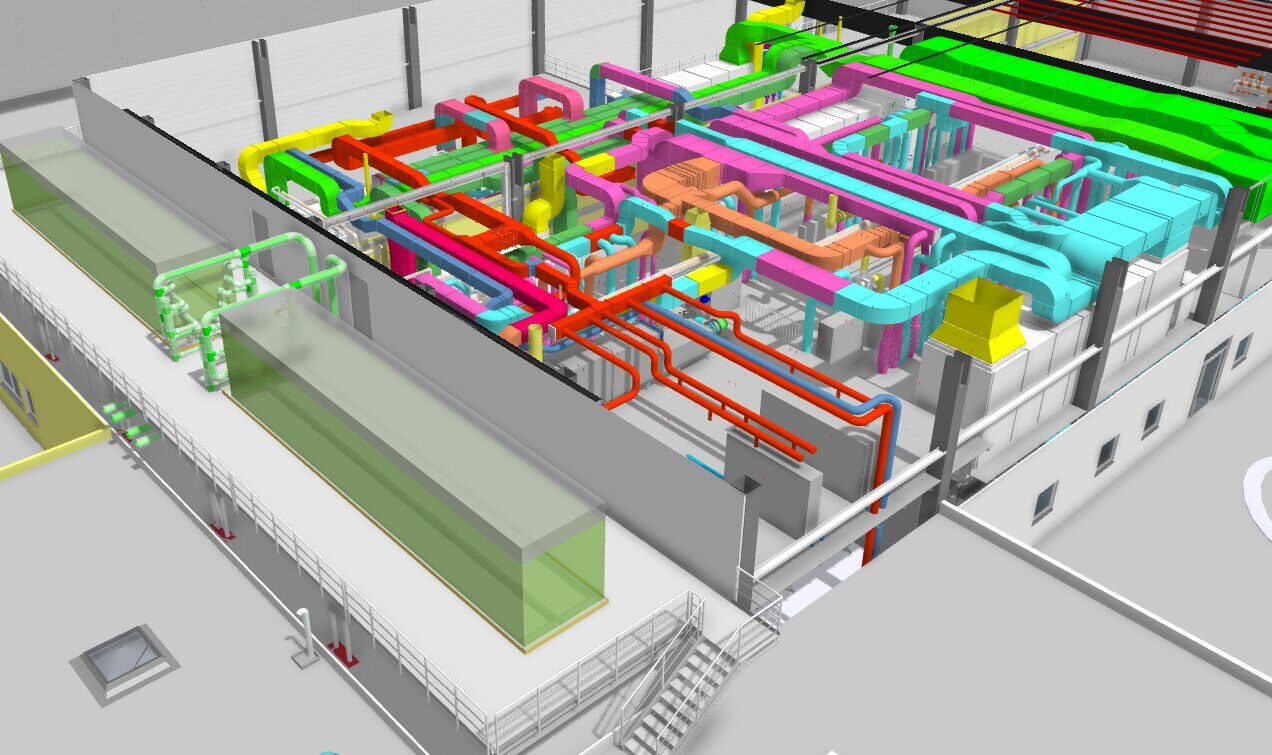
A blueprint for the future of building design
STÄBLEINARCHITEKTEN’s success story is a testament to the transformative power of digitalization in architecture and construction. By embracing innovative technologies like ALLPLAN and Imerso, the firm has not only overcome the challenges inherent in refurbishment projects but has also set a new standard for precision, efficiency, and collaboration. Their journey demonstrates the immense potential that lies at the intersection of architecture and technology.