In Nigeria, a significant infrastructure project is underway, with the Portuguese firm, Quadrante, designing the bridges along the route. Using the powerful design tools of ALLPLAN Bridge modeling software, Quadrante is designing a new 480 km railway line extending from Kano to Maradi and from Kano to Dutse. But this project is more than a simple transportation venture; it’s a testament to how innovative design software can drastically improve project efficiency and timelines.
Quadrante is setting a new benchmark in the industry by leveraging ALLPLAN Bridge to design 1 km long girder bridges in just two hours. This quick turnaround is crucial, especially considering the security concerns in the area. Their aim is not just to build a railway line but to execute the project with maximum efficiency and minimum delay, contributing to the successful – and rapid – completion of over 130 girder bridges.
Project Background
This project is a groundbreaking venture connecting Nigeria and Niger and is in the advanced stages of design and construction. Valued at USD 1.82 billion, this project covers procurement, construction, and project costs of a single-track, standard-gauge railway line spanning from Kano in northern Nigeria to Maradi in southern Niger. A branch from Kano extends towards Dutse, also in northern Nigeria.
In total, the rail line spans 387 km between the Kano to Maradi section, with the Dutse branch spanning an additional 93 km. The project also includes 20 railway stations, 5 maintenance yards and workshops, 52 railway bridges, 75 road overpasses, and 6 road underpasses. Given the project’s location in less populated yet security-sensitive areas of northern Nigeria, swift construction of all the project elements is necessary. The detailed planning aims to maximize construction efficiency while minimizing construction schedules to adapt to the terrain and logistical complexities. Quadrante is managing the detailed design aspects of the project, with elements such as bridges, overpasses, and underpasses being designed using Building Information Modelling (BIM).
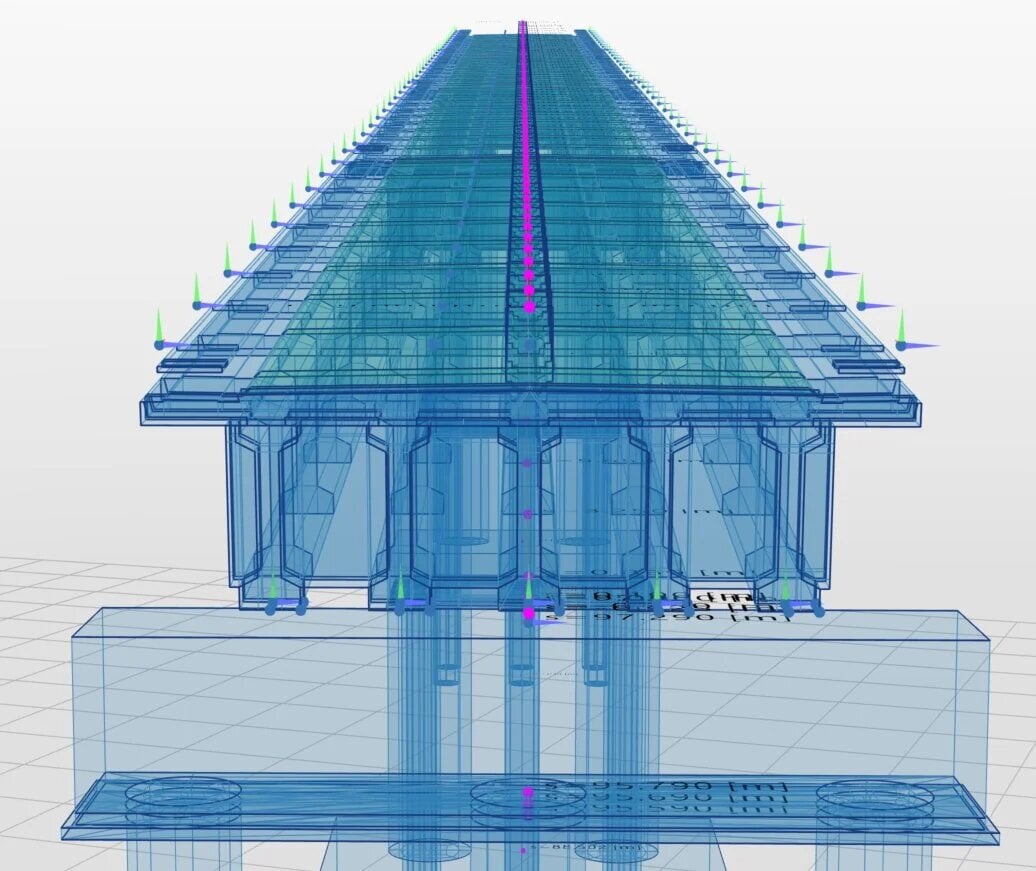
Standardization = Efficiency
When it comes to bridge design, Quadrante is remarkably efficient, in part due to their willingness to develop their proficiency with and knowledge of ALLPLAN Bridge. A template bridge model is created in ALLPLAN Bridge. This includes several unique elements such as vertical laminar components, which are used to produce Boolean operations, a form of calculation used to construct the joints between the prefabricated slab elements. In addition, this process also requires the import of the railway alignment from Bimplus using LandXML. The model uses reference lines, points, and different cross sections along the deck to create a comprehensive structure, taking into account minor changes in deck extremities and the positioning of rails and pedestrian paths.
For the 3D model, the main components are girders, piers, and link girders. The piers and abutments are produced for each support, with the latter being introduced by a SmartPart positioned reference point. The deck is essentially produced by link girders, which need to start at a reference point. These reference points are introduced using girder elements that are connected to the bridge’s main axis. The entire process results in independent link orders for each span. By using templates and Boolean operations, the joints between prefabricated elements are created. Despite the complex structure, the model is adaptable, allowing for quick transformations to adjust the dimensions of the bridge components. This model acts as a template for creating additional bridge models, with additional spans able to be quickly added with the help of a TCL file.
Once the 3D model is ready, the team moves on to extract 2D drawings for each bridge. The process is optimized to minimize the specific drawings from each bridge. Only three or four general geometry drawings are produced for each bridge, showing the bridge in its full length. Standardized drawings are used for details such as piers and foundations, which are parameterized based on elevation and height.
With this workflow, the team is able to produce a complete, rigorously defined model of a one-kilometer railway bridge in about two hours. The speed and precision of this design process, according to Quadrante, is unmatched by any other software or workflow. This is how Quadrante leverages ALLPLAN Bridge to set a new standard in bridge design efficiency.
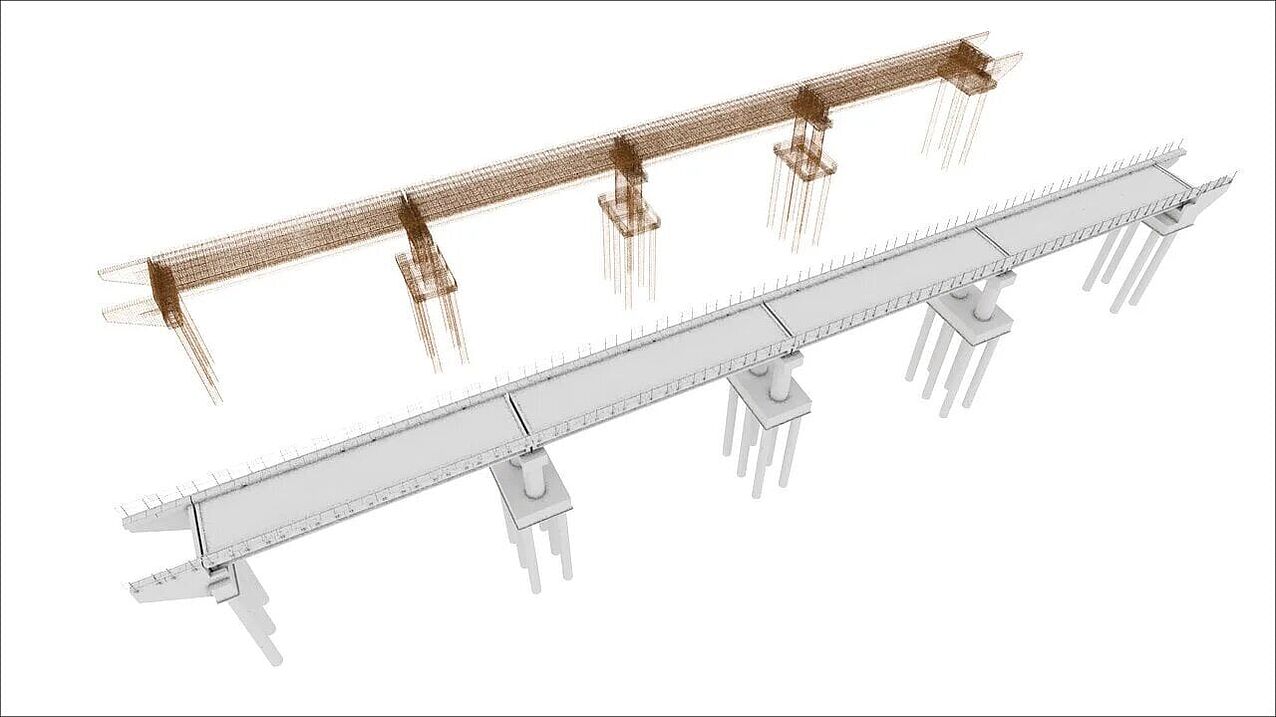
Rapid Modeling of Variable Elements
Quadrante’s application of ALLPLAN Bridge to design overpasses begins with their standard template. Most of these structures consist of three continuous spans, supported by prefabricated I-beams. They employ a prefabricated slab that serves as formwork for the final concrete deck, which assures an integral functionality of all deck components. A unique feature is the absence of bearings, as the beams rest directly on the pier caps and abutments, thus simplifying the design. Abutments are defined in ALLPLAN Bridge, except for transition slabs which are positioned using a reference point. To shape the prefabricated slabs, a model element is used as a ‘cutter’.
In terms of modelling, overpasses come with unique challenges due to their variable curvatures, depths, and asphalt layers. To maintain construction efficiency, Quadrante decided to keep the deck slab thickness uniform and achieve the vertical curve by varying the bituminous layer’s thickness. This is achieved by a Boolean operation between the deck and the asphalt layer, resulting in a variable thickness in the asphalt layer. The girders, abutments, and piers are then added to complete the structure. Despite similarities to the bridge modelling workflow, the overpasses require careful adjustment due to their distinct geometrical differences and vertical curvatures.
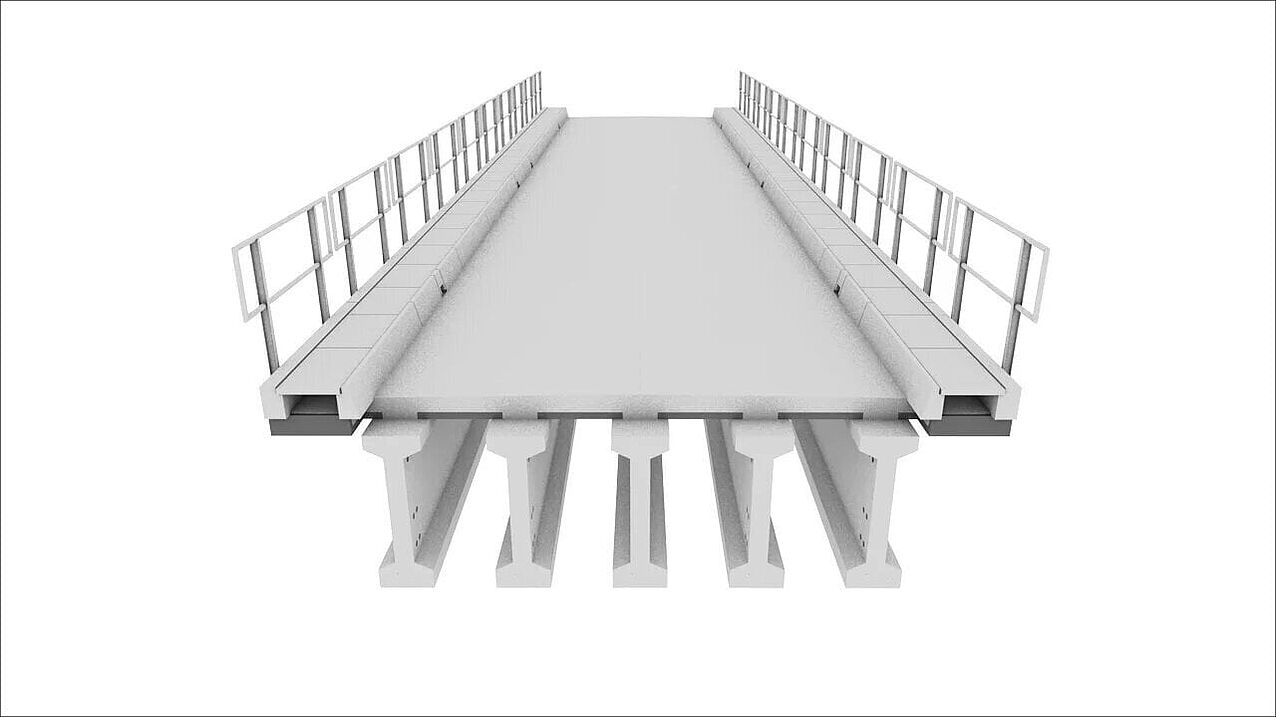
Visualization for Increased Confidence
Quadrante utilizes ALLPLAN Bridge in the modeling of underpasses and their surrounding terrain, providing a comprehensive visual representation of the project. To foster a comprehensive understanding of the solution among different stakeholders, they opted to model stretches of roads and railways alongside the underpasses. In this process, the team worked with a closed frame underpass of constant geometry. This included modeling elements like a closed cross section, the cross section for the retaining walls (without the top slab), the tapered concrete barrier, as well as the rails and blocks for the bridge.
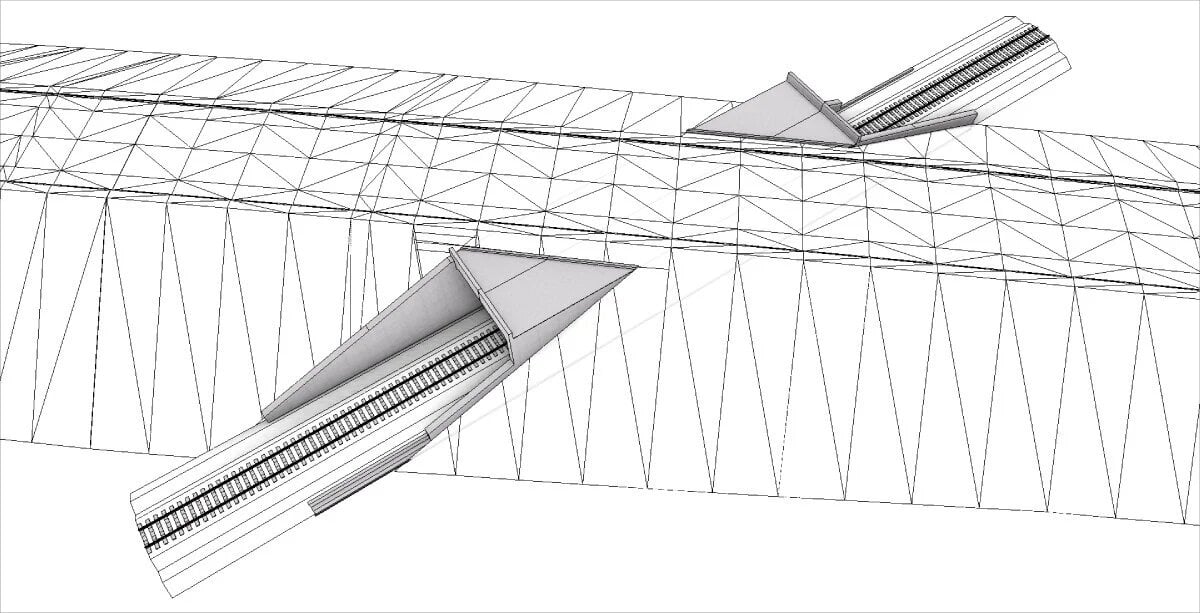
Efficient Reinforcement Modeling
As the bridges on this project are modular, Quadrante has been able to efficiently model the reinforcement with ALLPLAN. By modeling the reinforcement on one span and then reusing this throughout the project, significant time savings can be made while also minimizing errors.
However, it has other benefits as well – with all the project reinforcement modeled in ALLPLAN this way, it is quick and easy to generate accurate bar bending schedules in the format required by the client. As all the information is contained in the model, the schedules can be created with just a few clicks.
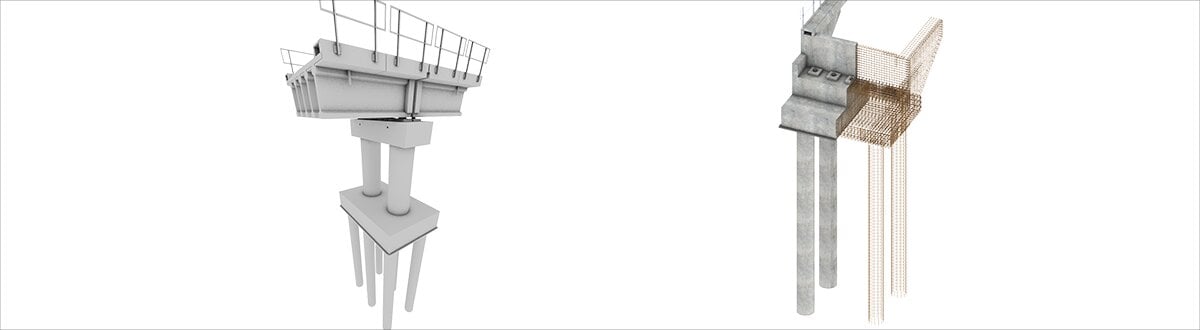
Pushing Boundaries
Quadrante’s groundbreaking approach in utilizing ALLPLAN Bridge technology demonstrates their commitment to pushing the boundaries of bridge design. By integrating ALLPLAN Bridge into their projects, from designing girder bridges, overbridges, to modeling bridge reinforcements and visualizing underpasses, they have achieved an enhanced level of design efficiency and accuracy. These advancements not only contribute to the successful delivery of complex projects like the Kano-Maradi-Dutse rail line but also pave the way for more innovative engineering solutions in the future.
See Quadrante’s process in action by registering to watch Quadrante’s presentation at the ALLPLAN Build the Future Infrastructure Digital Conference.