Experts from the construction industry predict a bright future for precast elements: the average annual growth rate of the global precast concrete industry is expected to be 5.3% between 2021 and 2028. In 2020, the precast concrete market was valued at around USD 92.14 billion and is anticipated to grow to over USD 139.33 billion in 2028[1]. However, the average growth rate of the construction industry as a whole is expected to be just 3.2% annually according to the Global Construction Report. Why industrialized construction in particular is growing faster than the rest of the construction industry can be explained by the numerous advantages of this technology.
Prefabrication offers fixed prices, on-time delivery, and precision
When prefabricated parts are used, building components are prebuilt to the millimeter in factories and then transported just in time to the construction site. There, a crane takes over the assembly and moves the precast elements to the right place.
What are the tangible advantages of industrialized construction? Off-site manufacturing transfers the benefits of industrialization to the construction industry and thus ensures greater efficiency, shorter lead times, and higher precision. Another major advantage is the extraordinary accuracy of cost and time planning – especially in view of the fact that, according to McKinsey, conventional construction projects usually take 20% longer than planned and cost up to 80% more. With precast projects, on the other hand, contractors benefit from fixed prices and reliable delivery dates. The reason for the high reliability is exact production planning and precise control of the production machines in the precast plant.
The production conditions also play a decisive role. For example, manufacturing parts in factories – which are completely unaffected by the weather – guarantees a consistently high quality standard for the precast concrete elements. The right software ensures that the raw materials used are optimally measured and that reinforcement quantities can be significantly reduced compared to in-situ concrete.
Resource-efficient construction thanks to precast elements
Precast concrete elements also score in terms of sustainability: concrete consists of 100% natural materials that are ideally extracted and processed in close proximity. In addition, this building material can be almost completely recycled and used for road construction, for example. Moreover, research is constantly developing new ways to further reduce the ecological footprint of concrete and cement in particular. Thanks to the shorter construction time, local residents benefit from reduced noise and dust pollution. Precast concrete also has outstanding durability and is highly fire resistant.
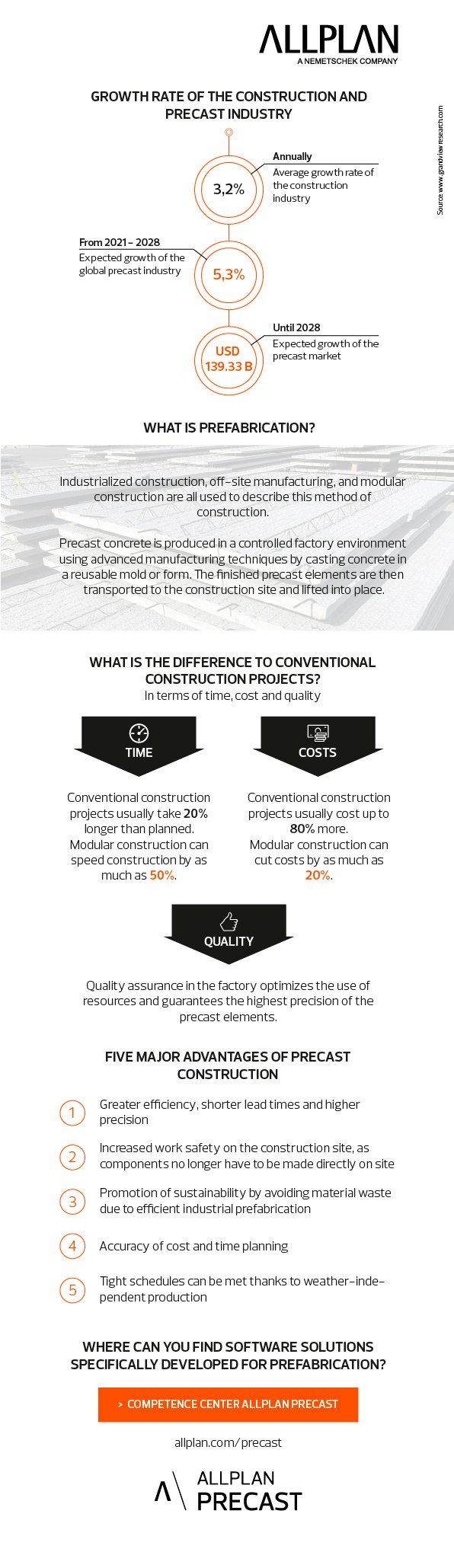
Specialized precast design software from ALLPLAN
Industrial prefabrication of elements enables the construction industry to experience the productivity gains that the automotive industry has been significantly benefiting from for years. It is no wonder that thought leaders like Tesla have long relied on precast elements to build their new production facilities. The precast industry can thus serve as a role model for the digitalization of the entire construction industry.
However, new ways of designing also require rethinking in terms of suitable tools. Therefore, a reliable software partner that specializes in the design and detailing of precast elements is of the utmost importance when it comes to such a transition. The experts from the Competence Center ALLPLAN Precast are very familiar with the special requirements of the precast industry and have therefore developed their software solutions ALLPLAN Precast and Tim specifically for precast projects. Read more about how ALLPLAN Precast enabled construction projects like the Rapid stadium in Vienna to be finished on time here.
[1] Source: Market Analysis Report, Februar 2021, www.grandviewresearch.com/industry-analysis/precast-concrete-market