In Kynšperk nad Ohří in the Czech Republic, a new bridge will soon replace the existing level crossing. Not only will this enable the separation of the road and railway traffic, but the existing road alignment could be improved at the same time to provide a safer and more comfortable ride. The new seven-span bridge will have a total length of nearly 145m, with a 27.5m span over the railway. The bridge, which was designed by Sagasta s.r.o. engineering consultants, is one of their first projects designed entirely in 3D using ALLPLAN Bridge and exploits the benefits of parametric bridge design.
Design Background
The new bridge was designed using prestressed concrete slabs for the bridge spans, which vary in length from 15m to 27.5m. The main span is supported by piers, while the rest of the bridge sections are each supported by two bearings. The central span that crosses over the railway includes a precast concrete slab supported by steel beams, which acts as the formwork for a cast in-situ reinforced concrete slab on top. This unusual construction method and composite design ensured that no formwork was required over the railway during construction, reducing the disruption to the operation of the railway.
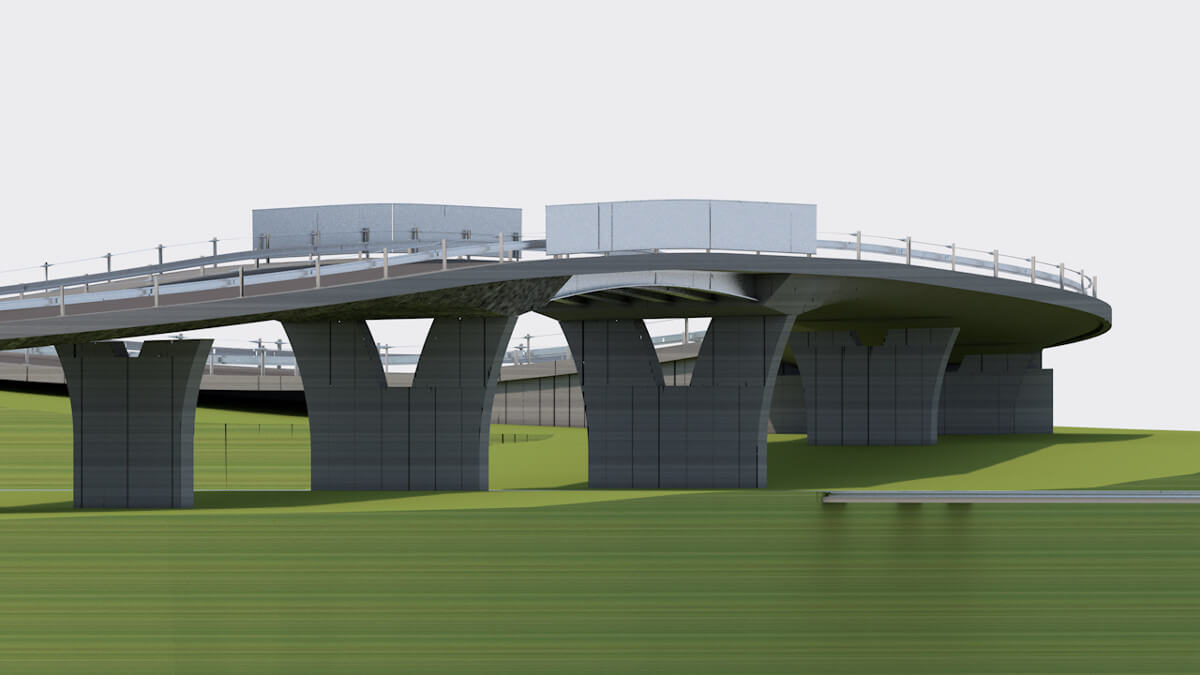
3D Bridge Modeling Using Parametric Design
Several different road alignments were designed to determine the best option of the new overpass. The horizontal and vertical alignments of the bridge were then imported into ALLPLAN Bridge in .xml format, giving the bridge engineers the data they needed for their design. From this base, the rest of the bridge – including the bridge structure, road, cornices, safety barrier, piers, and retaining walls – were all designed parametrically in 3D using ALLPLAN Bridge.
Parametric design was used due to the large number of structural members involved. This made designing the cross-sections much easier, as each parametric cross-section had variables assigned such as length or angle. For each variable, longitudinal profile stations were assigned which linked to the vertical alignment of the bridge. This way, the cross-sections could be designed and adjusted easily and then the road and bridge structure could be swiftly designed by extruding the cross-section along the alignment.
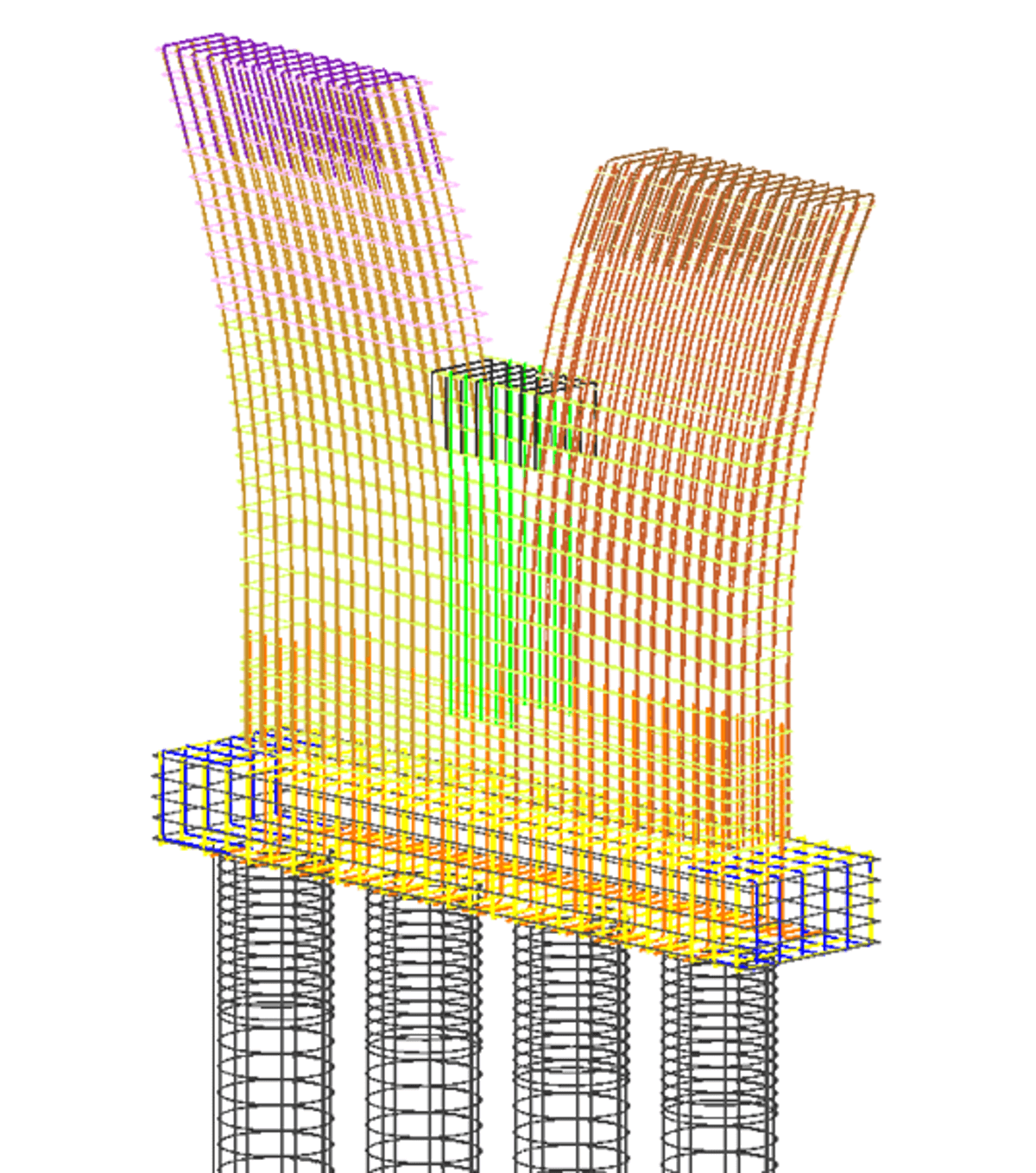
Parametric Bridge Design Benefits
The main span uses six steel beams to support the lower concrete slab. Creating this cross-section was as simple as creating one parametric cross-section of one of the steel beams, and then replicating it for the other five beams. Designing it parametrically enabled variables to be included, such as the distance of the beam to the road axis, the beam height and width, the height of the precast slab, and the height and angle of the roadway. This way, the cross-section could be adjusted as required and the linked variables would also update, saving valuable design time and reducing the risk of errors.
The benefits of parametric bridge design include more than just updating the cross-section. The road alignment was changed several times, as well as the design of the initial four different variants. Every time the road alignment was updated, the bridge needed to be moved to the correct position. This was done automatically by the software, but the stationing would then need to be updated as well. The designers used a text file with the correct stationing, which was originally created in Microsoft Excel and then copied into ALLPLAN Bridge. Changes of the span length or other variables were quick and easy to do in Excel and then update in ALLPLAN Bridge, with linked variables updating automatically.
After the bridge design was completed, the bridge model was exported into ALLPLAN Engineering for completion. Here, the concrete reinforcement could be easily modeled, the documentation such as general arrangement drawings created, and visualizations of the completed bridge generated.
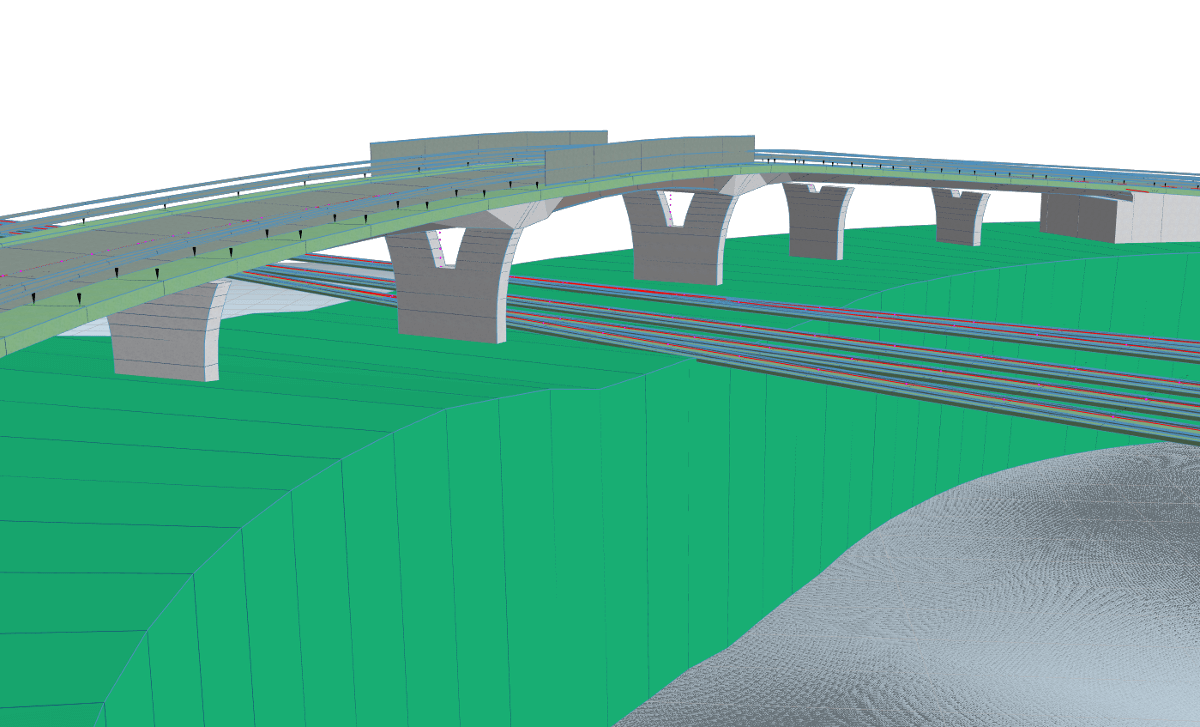
Conclusion
For the designers at Sagasta, 3D bridge design using ALLPLAN Bridge offers a number of compelling advantages. “While 2D drawings are good for easy construction, with a 3D model the design is much more precise – there are no collisions between structural members or reinforcement, and it is much easier to visualize the complex details. Any edits are much easier as any changes to the model are updated automatically in the drawings – and for bridge design, these two advantages are some of the most important,” enthuses Ladislav Lidmila, Bridge Engineer at Sagasta s.r.o..
Try a free, 30-day trial of ALLPLAN Bridge – ALLPLAN’s groundbreaking bridge design software – to see how much more efficient bridge design can be.
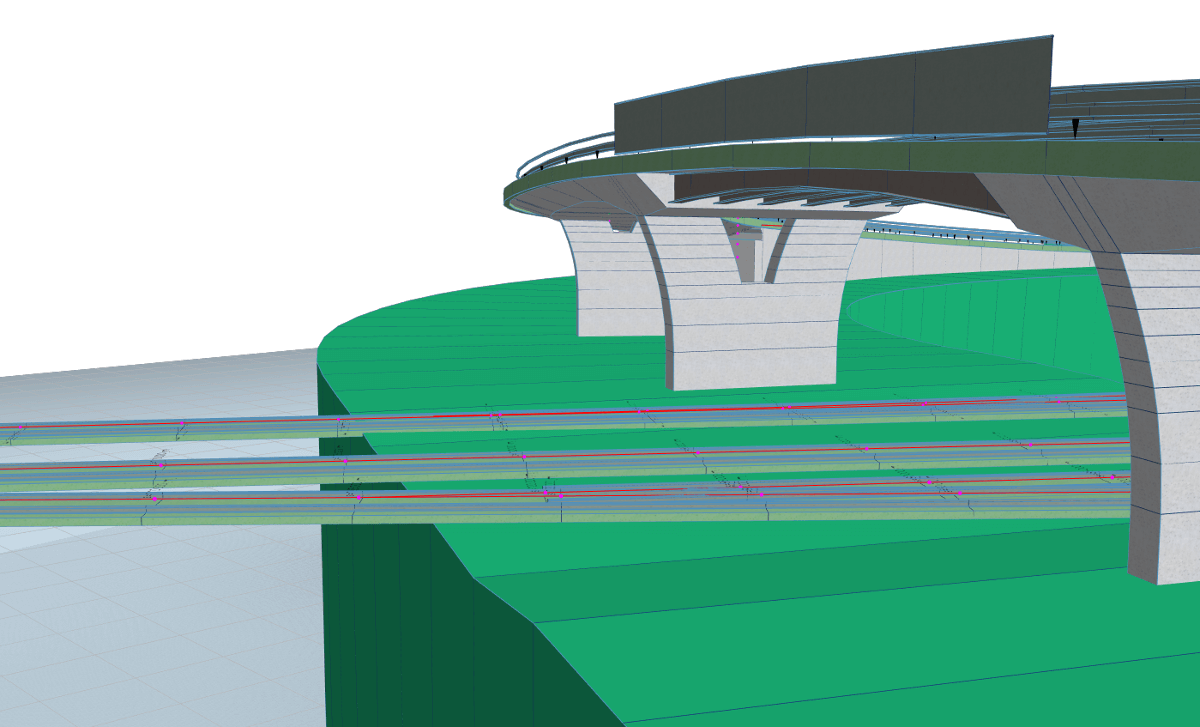