The world’s tallest man-made structure – the Burj Khalifa – is a construction project with an interesting story to tell. Towering at 828 meters, it has been a symbol of Dubai’s ambition and innovative spirit since its inauguration in 2010. Constructed by Emaar Properties, the Burj Khalifa surpassed all previous architectural benchmarks, creating a spectacle that can be seen from nearly 100 kilometers away.
Despite the emergence of other tall buildings such as the Taipei 101 tower and Malaysia’s Merdeka PNB 118, Burj Khalifa continues to hold its crown. Thanks to Théo Dudermel, also known as Looking 4, we delve into the unseen facets of this iconic skyscraper, offering insights into the unique challenges faced during its construction and how the architects and engineers involved overcame them.
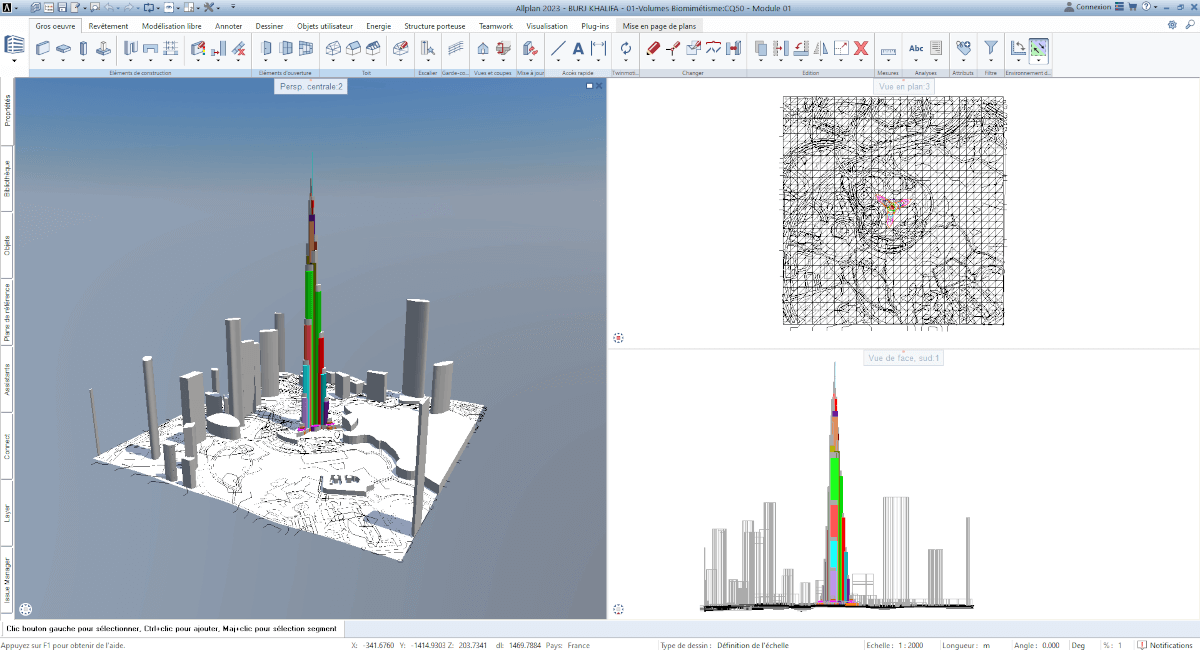
Technical Challenge #1: Countering Wind Forces
Constructing a structure as monumental as the Burj Khalifa presents a myriad of technical challenges, overcome through the collaboration of architects, engineers, and contractors. A key challenge was designing a building capable of withstanding the immense wind forces acting on such a towering structure.
The solution was found in nature and architectural history. Adrian Smith, inspired by the local desert flower, the spider lily, devised the Burj Khalifa’s tripod base, utilizing the flower’s geometric properties for structural strength and wind resistance. Moreover, Smith and his Chicago-based team drew inspiration from the 1968-built Lake Point Tower in their home city. This design not only assures stability but also lends an elegant aesthetic to the tower. The Burj Khalifa’s tapered profile was rigorously wind tunnel-tested over 40 times during the design phase to validate its wind resistance.
The structure’s resilience can also be attributed to its 27 spiral intermediate levels that ascend towards the top. As articulated by Skidmore, Owings, and Merill’s chief engineer, Bill Baker, these levels play a vital role in wind management. If the tower is subjected to strong wind vortices, it allows the structure to pivot without the risk of damage. Furthermore, these intermediate levels accommodate terraces at regular intervals, adding functionality to their structural purpose.
A less noticeable but essential aspect of the tower’s design is the central concrete core, fortified at the base by three large buttresses. This configuration significantly enhances the stability of the building. The effective combination of the tripod base, intermediate levels, and buttressed core ensures the tower can bear its weight and resist extreme weather conditions, including violent winds of up to 250 kilometers per hour. Even in such high winds, the tower’s peak shifts by a maximum of only two meters, showcasing its remarkable stability.
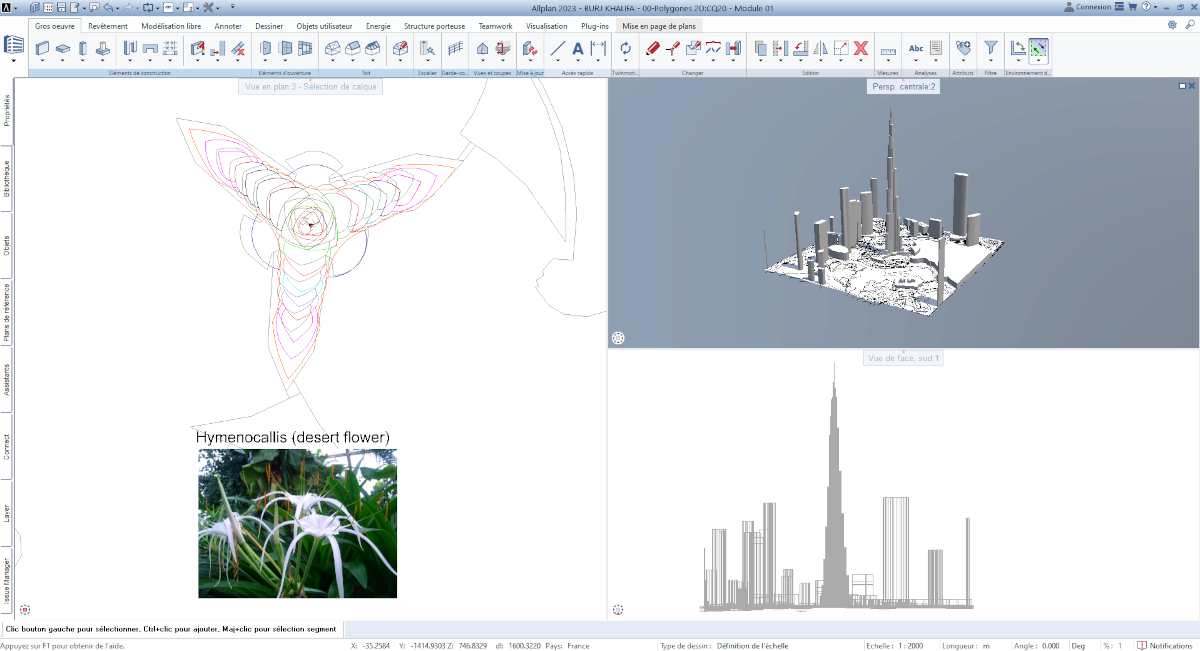
Technical Challenge #2: Constructing Firm Foundations on Sand
The construction of Burj Khalifa necessitated a robust foundation capable of bearing its enormous weight, especially given the complex geomorphology of Dubai’s terrain – predominantly composed of a 40-meter-thick sand layer before hitting stable bedrock. The task was to reach this solid ground to anchor the 500,000-ton tower securely.
To this end, substantial holes were drilled into the sand to house a network of colossal concrete pillars. A total of 192 piles, each 43 meters long and 1.5 meters in diameter, were embedded 50 meters deep. Resting on the rock bed, these high-performance concrete pillars effectively underpin the immense four-meter-thick slab forming the tower’s base. Ultimately, the construction of these foundations required 110,000 tons of concrete, equivalent in weight to the largest active aircraft carrier in the U.S. Navy. These were the deepest foundations ever constructed at the time, later surpassed by the neighboring Dubai Creek Tower in 2017.
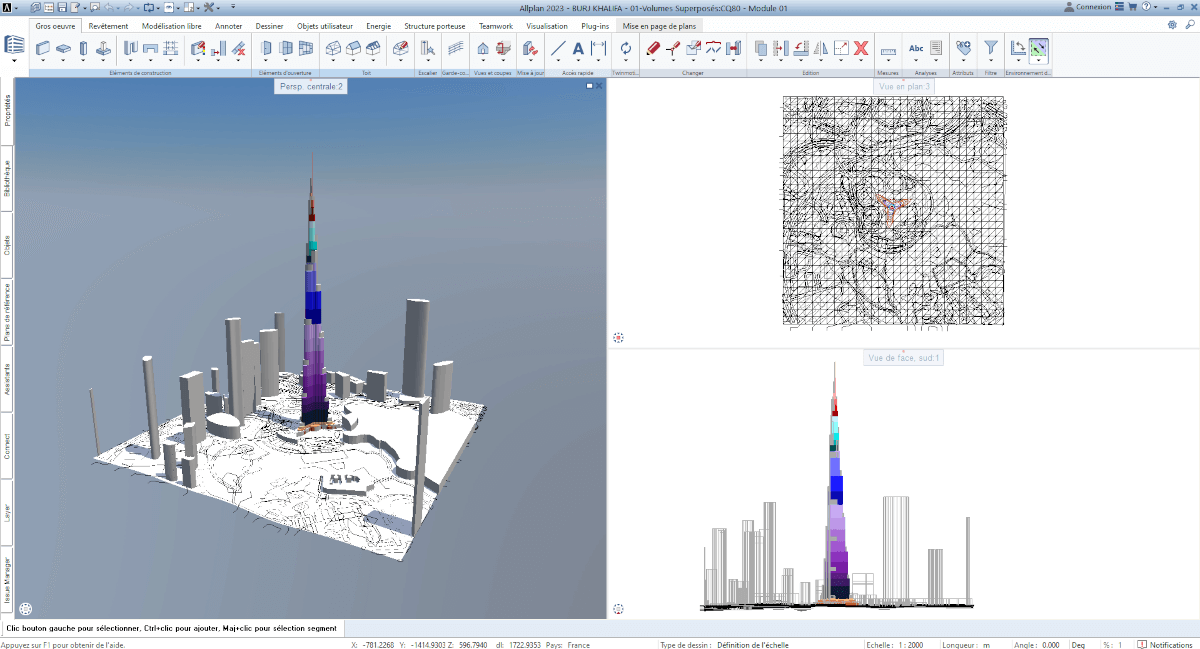
Technical Challenge #3: Constructing in Extreme Heights and Temperatures
Managing the colossal delivery of materials and orchestrating this Herculean project presented significant challenges. At peak construction, over 12,000 workers were engaged, contributing a total of 22 million hours to the project’s completion. Additionally, almost 330,000 cubic meters of concrete had to be transported to the site and hoisted to create the highest floors.
The solution involved developing a special brand of concrete capable of enduring temperatures exceeding 50 degrees. Due to Dubai’s extreme daytime heat, concrete pouring had to be conducted at night, mixed with ice to prevent premature solidification.
Numerous other innovations contribute to the building’s ability to deal with extreme temperatures. The building’s cladding required 142,000 square meters of glass across more than 28,000 panels. The glass was specially designed to reflect the sun’s rays effectively, preventing excessive heat transfer into the building. Given the tower’s vast glass surface, it takes maintenance teams between three to four months to complete a thorough cleaning.
Summing up the Feat
The Burj Khalifa stands tall today, a testament to the remarkable work of architects and engineers who overcame an array of structural and logistical challenges. Its tapered and angular design, specifically created to resist violent winds, exemplifies their ingenuity. Their ability to innovate and employ new techniques is what allowed them to successfully construct this colossal glass and steel titan.