The Cost of Construction is Rising – Here’s How Smart Digital Tools Can Help
KIBAG has gained numerous positive insights from a BIM pilot project in Zurich, in which work was (almost) exclusively model-based.
With around 60 locations and around 2,000 employees, KIBAG is one of the leading companies in the Swiss construction and building materials industry. The almost hundred-year-old family business has a broad base: In addition to 14 gravel and 25 concrete plants, KIBAG operates 17 construction, specialty and service companies with an extensive portfolio of construction services. In the latter, KIBAG Infra plays a decisive role as the central technical office. At the Build the Future ALLPLAN Summit 2024, Daniel Hasler (civil engineer SIA / project manager) used a pilot project to show what the office has learned from the (almost) universal use of BIM in specialist civil engineering.
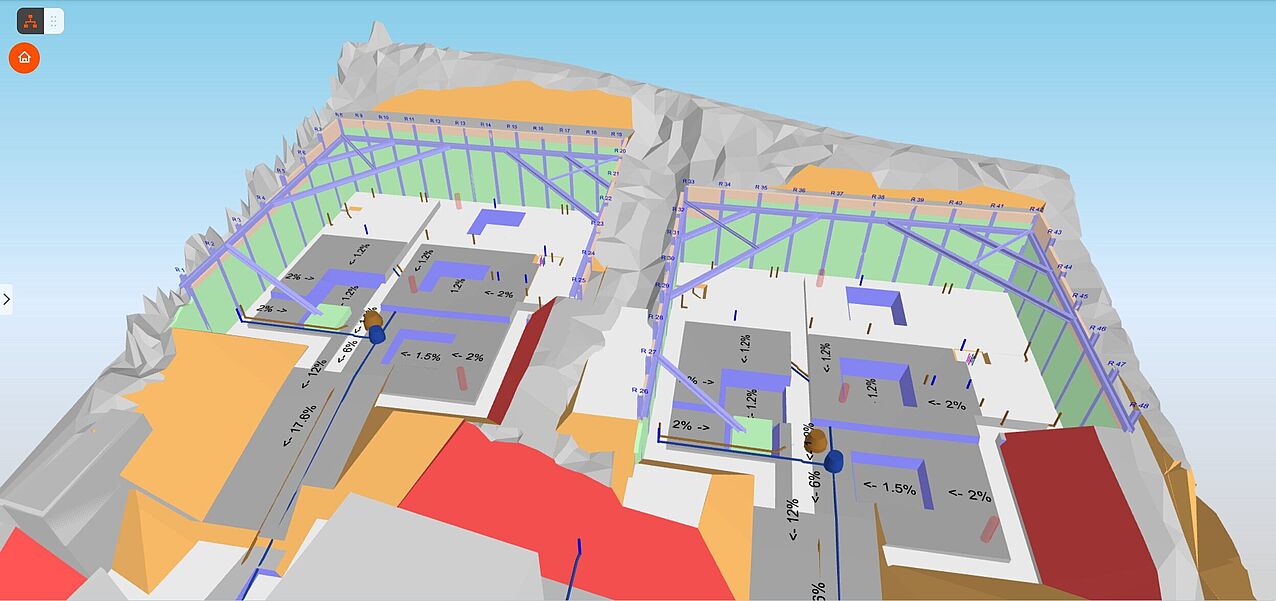
KIBAG Infra has already been working with BIM to a high degree for several years. However, the Segantinistrasse project in Zurich was the first to be realized almost completely model-based. The project involves the construction of two new apartment buildings with underground parking. The site is located on a slight slope in a heavily built-up area above the city. An embankment running between the two buildings posed a particular technical challenge. Due to previously relocated utility lines and a right of way for third parties, this had to remain and be included in the excavation support.
BIM2Field, 3D machine control, material orders and target/actual comparisons
For the excavation planning, the client provided an architectural model of the buildings, together with a proposal for securing the excavation. KIBAG Infra further developed the latter into a braced soldier pile wall. The conceptual planning during the tender phase - as well as the static calculation of the support - was initially carried out as standard using 2D static programs without reference to the model. However, the relevant verification sections could already be verified after initial modeling.
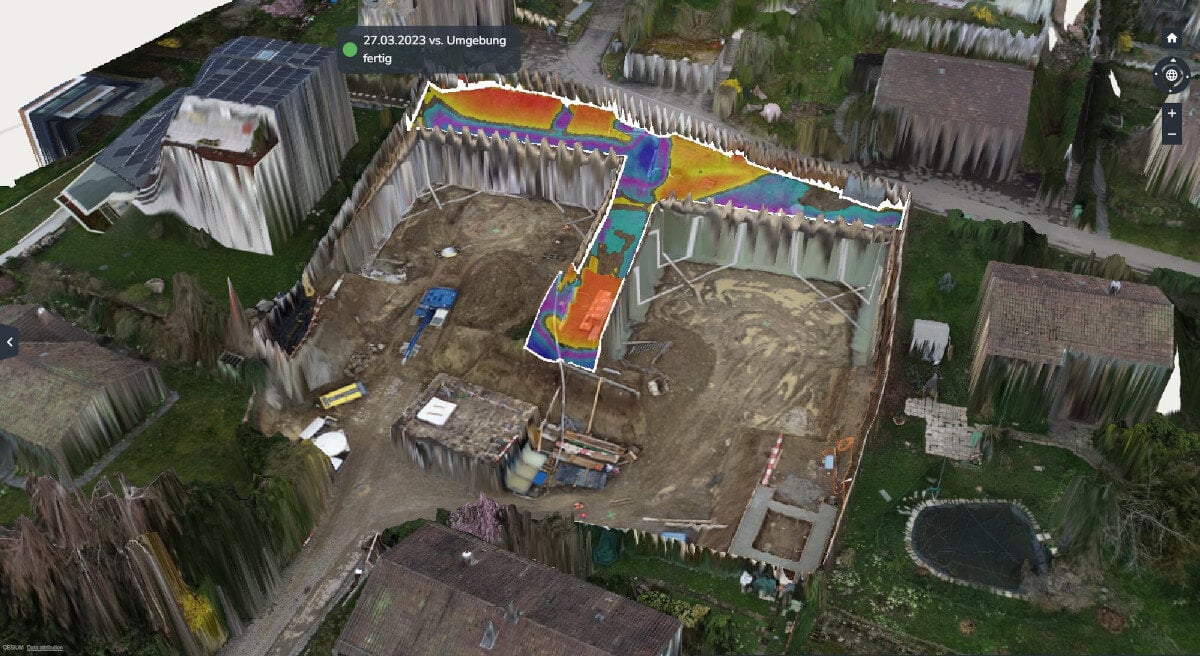
BIM2Field was executed using a "BIM container", which enabled a largely paperless construction site. The container can be used in any weather and can be easily (re)positioned using an excavator or crane. Thanks to the digital plan house, the execution model could be accessed directly on site via Bimplus. A printed plan (derived from the model) was only available as a backup, but was only used by subcontractors who had not been specially trained by KIBAG in using the model. The execution model was also used to prepare the 3D machine controls for the excavators, as well as the dimensions for material orders and a target/actual comparison.
New terrain data by drone
As two buildings had recently been demolished on the site, which was very difficult to access, and new utility lines had been laid, among other things, both the public geodata and the client's as-built data were no longer up to date. For this reason, KIBAG created new drone images of the terrain for further modeling. Based on the structural model of the structural engineer, which also included the surrounding walls, KIBAG Infra was able to model the excavation pit with the contractor's variant of the excavation pit closure.
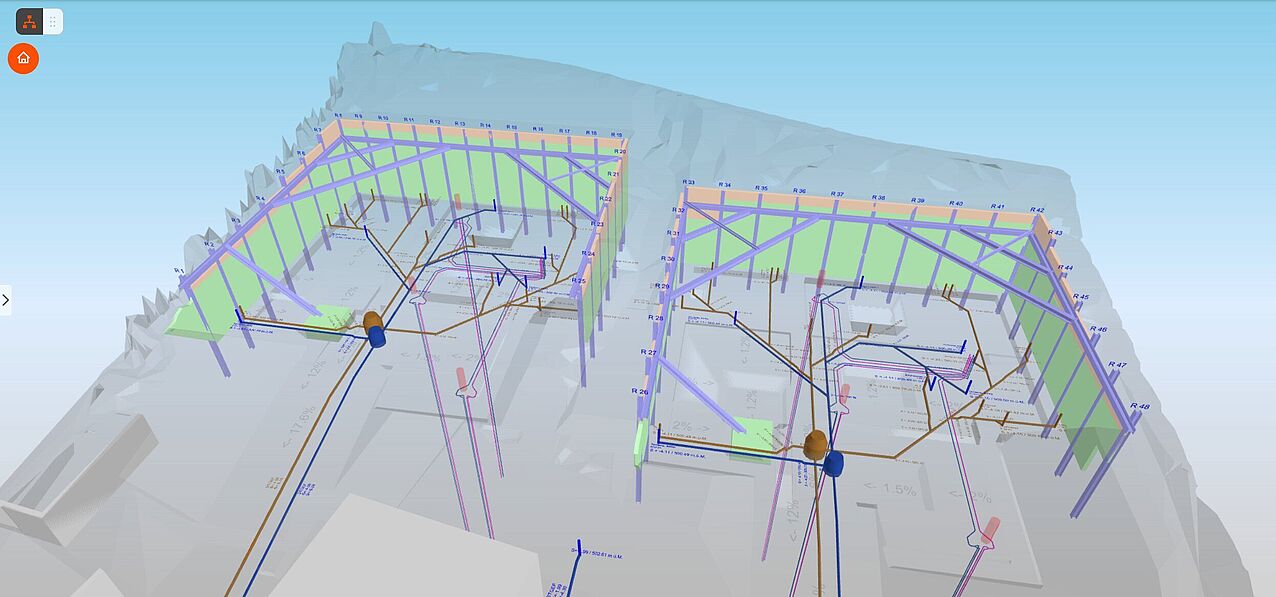
Communication via Bimplus
During the planning phase, there was a lively exchange between the modeler and the civil engineer at KIBAG Infra. This was deliberately carried out mainly digitally via Bimplus in order to establish location-independent processing for future projects. The foreman was also involved in the execution planning in order to define what should ideally be recognizable in the model and what information it should contain. For example, at the foreman's request, the numbering of the beams was integrated into the model using 3D text.
The foreman was able to read out or measure the required dimensions or stakeouts directly from the model. The model was always accessed via Bimplus using the container or mobile devices (tablet or smartphone). Issue management in Bimplus was primarily used for questions. At the same time, the current construction site status was recorded via the BIM platform, so that the site management in the office was always aware of the status of execution.
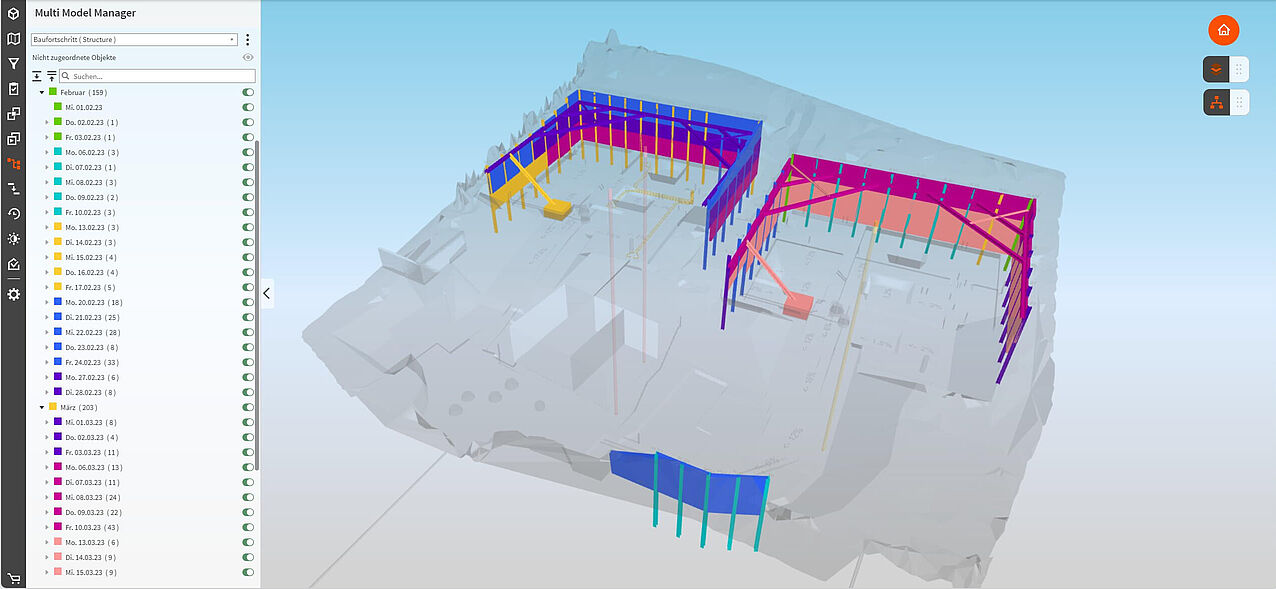
As much as necessary, as little as possible - lessons learned from the BIM pilot project
Model-based construction (BIM2Field) was very well received by the senior site personnel. In fact, the foreman was so impressed by the model that he immediately requested modeling of the service lines, which were originally planned in 2D. The direct communication via Bimplus between the responsible planners and engineers proved to be similarly successful. In addition to this positive feedback from those involved, Daniel Hasler highlights three specific lessons learned from the pilot project:
1. Every component, be it the lean concrete cleanliness layer, a specific use of materials or even their staging, must be modeled so that it can be used accordingly (for example in progress tracking).
2. Certain information, such as the numbering of components or gradient information, must be visually visible directly in the model (e.g. as 3D text) in order to facilitate execution. However, the following applies: as much as necessary, as little as possible.
3. A stable internet connection is extremely important, as connection interruptions lead to problems (such as different planning statuses) in cloud-based communication.
KIBAG Infra intends to expand its BIM applications even further in the future. This includes, in particular, feeding construction site data back into the model or linking the model and calculation via a standardized automatic classification of IFC models.
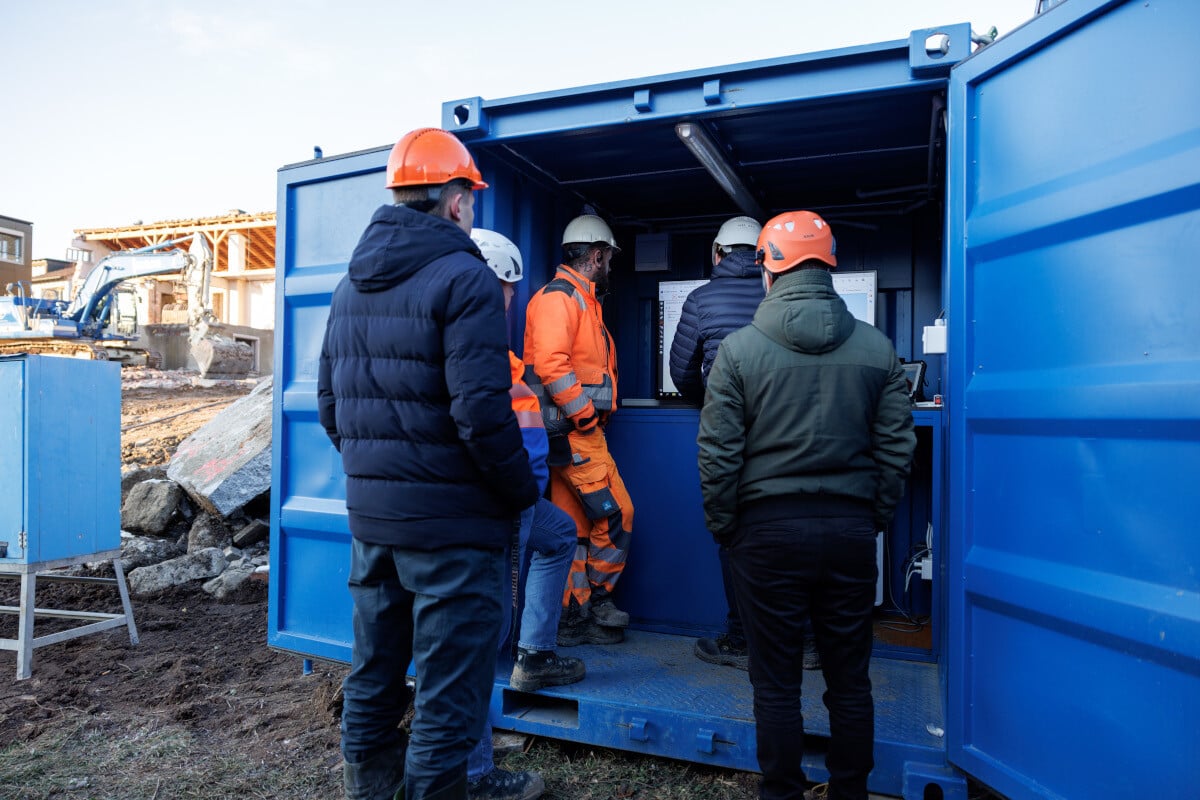